- +1
为好奇号着陆保驾护航的工业软件,如何在机器领域大展拳脚?
2012年8月5日,当造价25亿美元、重达900公斤、接近小型轿车大小的“好奇号”探测车进入火星大气层时,这个配备顶尖技术的大家伙还在以2.1万公里/小时的高速向前飞行。由于火星的大气层密度只有地球的1%,“好奇号”穿梭这层稀薄的大气时,必须在短短7分钟内自行将时速从约2万公里骤降至零。否则,这一史上造价最昂贵、设计最精密的行星探测器将与火星相撞,游戏结束。
对于造价数十亿美元的航天器而言,最关键的莫过于精确性。在被NASA(美国航空航天局)工程师们称作“恐怖7分钟”的“好奇号”着陆过程中,所有设备和程序不容闪失。而这一切,必须由计算机独立完成。生死攸关的7分钟,实则是演绎了8000次虚拟模拟之后得出的最佳方案。
“在‘好奇号’的任何一个实体部件被制造出来之前,就已经完成了全部的设计、模拟仿真和验证过程,也就是说,在每一美元被用于实际生产之前,所有的数字化设计模拟仿真过程都已经在软件里被实现了。”回忆起这项航天创举,西门子PLM Software制造工程软件业务高级副总裁Zvi Feuer依然兴奋不已。西门子产品生命周期管理(PLM)软件是“好奇号”系统开发和测试的幕后功臣,“我们的软件能够保证,当这个东西真的被生产以及被发射到火星上时,每一个要求的动作都能够精确实现。” Zvi Feuer对澎湃新闻(www.thepaper.cn)说。
如今,这套确保探测器各部件完美协作的软件系统被广泛应用于工业世界,执行不同操作任务的机器人被安上了“大脑”、产生“对话”,虚拟世界与真实生产空间得以实现无缝通信。


“好奇号”的幕后功臣
无论是探测车的设计、搭载的技术与装备、担负的任务还是降落着陆的方式,“好奇号”都堪称火星探测史上最具野心的计划。为使探测车平稳着陆,防止为寻找生命化学成分而设计的装备受损,探测车必须分毫不差地执行数百个步骤的复杂操作,并且整个过程没有人工干预。任何一个细节出错,所有前期投资与努力瞬间化为乌有。
但问题是,在大气密度高出火星100倍的地球,这个过程根本无从演练,唯有借助虚拟平台模拟火星环境。负责推进“好奇号”项目的NASA喷气推进实验室(JPL)利用西门子的模拟软件对火星探测器进行数字化设计、模拟和虚拟组装,以便后续制造样机。提到西门子,人们总是很容易联想到德国精良的硬件设备,其实,这家工业自动化领域的巨擘本身也是工程软件巨头。利用模拟技术,从概念设计到详细的部件设计,从组装到测试,一切都事先在虚拟世界中完成。模拟软件成了探测器从虚拟世界通向现实红色星球的桥梁。
比如,由于“好奇号”火星车重量太大,无法使用常规的安全气囊着陆,工程师们专门设计了“空中吊车”,帮助探测车在降落的最后阶段减速,缓缓降落到火星表面。着陆之后,“空中吊车”将脱离“好奇号”。

参与该项目的NASA工程师Anita Sengupta在一段视频中说:“我们不能在‘好奇号’距离地面很近的时候点燃火箭。因为在这种情况下,火箭将形成巨大的尘云,破坏‘好奇号’的机械装置和仪器设备。”
于是,研究人员利用PLM软件对“空中吊车”火箭引擎的火苗扩散情况进行了模拟,以确保火苗不会烫坏探测车或用于固定探测车的套具。“不仅吊索要能分毫不差地降下探测车,确保探测车不会受到火苗干扰,同时还有一条类似于脐带的线缆连接着探测器和吊车,在分离时间点上吊车升起的时候才会断开。所有这些线缆都必须同时断开。为实现这一点,我们布置了很多小型切割器,它们必须同时切断所有线缆。上述这些过程都是通过我们的软件来模拟的。”负责NASA项目的PLM客户主管Joel Rooks介绍道。
如何控制这一庞大工程的各个部件相互协调避免碰撞,是摆在工程师面前的另一道难题。“好奇号”整套设备包含约9万个专门制造的部件,其中很多与设计规格的容差只有100微米,这大约相当于一根头发丝的直径。最复杂的并非火星探测车本身,而是整个探测计划中各个系统单元的整合。这就好比,要制造和控制单一部件并不难,但要使整个复杂系统有条不紊地运转,难度和工作量远远高于单一部件的累加。

更苛刻的是,为尽量避免浪费空间,所有部件必须合拢到一个极其拥挤的包中,但是同时又要留出发射和返回时剧烈晃动的摆动空间,以及在高达1648℃的温差下不同材料的热胀冷缩空间。“要设计可以如此紧凑布置的部件,需要新的功能和技术。”NASA火星探测计划负责人Doug McCuistion博士说,“我们采用了西门子的很多系统,来帮助我们完成这些工作。”
“鉴于每个部件涉及不同的材料,确保做到这一点的唯一方法,就是针对每个部件构建一个有限元素模型。利用这种方法,我们将复杂的表面划分成很小的元素,然后根据元素之间的关系来计算元素。” PLM解决方案部的顾问Kent Rash介绍说。
通过这种模拟,工程师可以在仿真环境下对各种规模的装配组合进行动态测试,比如模拟测试探测器着陆,从而计算出着陆时对整个探测器结构产生的应力。同时,采用数字模型,并配合计算机数控,可以使部件生产实现超高精度。据介绍,“好奇号”整个系统的整合,一共使用了50万行计算机代码,令其在极端的火星环境下全自动地进行工作。

用逻辑武装工业机器人的大脑
看中虚拟化模型设计与仿真测试的不止NASA一家。精确、高效、降低出错率、严控成本,同样是所有制造型企业的普遍诉求,尤其对于那些数字化生产的热衷者与先行者而言,软件带来的效益提升,在效率和直观性上远胜于硬件的更新换代。
一个常见的情景是,同一个工位上配备多台工业机器人,它们负责不同任务却又要相互协作,如何确保张牙舞爪的机械臂不打架?想像一下,若要在现实物理环境下进行调试,画面未免有些惨烈。但置于虚拟软件环境下定义任务并进行调试,相当于事先给机器人安上了“理智的大脑”。

“机器人可以进行交流。问题的关键在于,如何在作出投资之前,确保机器人在正确的位置上有序地操作?” 西门子PLM Software制造工程软件业务高级副总裁Zvi Feuer对澎湃新闻(www.thepaper.cn)说。生产流程的顺畅性、尽可能减少停机时间,对于生产者而言至关重要。
“机器人工作单元的设计中可以分成三部分,10%的重要性放在路径规划,10%的重要性放在虚拟调试,80%放在逻辑化编程方面。当然有好几个机器人一起工作的时候,每个机器人其实都有一个单独的控制器,单独的控制器可以是一个PLC(可编程逻辑控制器),整个工作单元都可以是一个PLC。” Zvi Feuer解释说,基于自动化编程控制,不同机器人之间可以避免冲突与碰撞,在有限空间内各司其职。
“对于机器人,许多人将所有注意力放在(单个)路径规划上。” 但若面对的是一个庞大的生产系统,这就略显不足。Zvi Feuer对澎湃新闻(www.thepaper.cn)说,西门子设计的所有流程都基于逻辑化编程。这不仅涉及单个机器人,还有多个单体之间的互联,并在此技术上进行虚拟调试。
所谓虚拟调试,就是在完成设计和逻辑化编程后,运用虚拟调试验证程序的可行性。所有这些,都是建立在高度精确的数字模型(digital twin)上实现的。有了数字模型之后,工程师就可以预测机器人在现实生产环境中是如何彼此接触的、运动路径如何。获取这些数据后,再进行逻辑编程,继而在现实中做测试,就可以防止机器人之间出现不必要的碰撞。
换言之,在数字化定义下,执行不同操作任务的机器人“知晓”彼此间的安全距离,一旦闯入对方安全区,机器人就会自行向对方发红色警报“当心哦,我正在进入你的安全区域”,另一个机器人则会回答说“好的我知道了”。这就是发生在逻辑化编程下的情境对话。
人机协作时代的再定义
“打个招呼吧,这位是你的机器人新同事。”不久的将来,或者说就是现在,越来越多的老板会对你这么说。人机协作时代的到来,拆除了挡在人类与机器人之间的安全隔离网,使得人机得以并肩工作。机器人真的会杀人吗?除了那些真正在生产线上与轻型协作性机器人一起工作过的工人之外,许多人似乎对机器人的安全性始终存疑。
“首先要确定人和机器人之间的安全区域,然后改进机器人的逻辑编程,让两者可以在自己相对安全的区域内独立工作。第二就是传感器,有了先进灵活的传感器之后,在人机危险接触之前就会进行提示。” Zvi Feuer认为,假如只是一台协作性机器人在生产线上工作,那没问题。若是人机混合产线,或者今天是人工产线明天又要换成人机混合产线,在逻辑编程上就要复杂得多。这种情景并不遥远,数字化制造时代越来越强调灵活生产。
“在这种既有人类又有机器人的生产线上,很多时候机器人的一些动作或是指令,变化是很多的,不仅有安全系数的问题,也有实时修改机器人路径等方面的问题。这些问题更加突出了逻辑编程的重要性。有了逻辑编程之后,才能够做一些实时的修改和优化。” Zvi Feuer说。
新技术的发展,正呈现出机器人领域新的可能性。Zvi Feuer认为,可视化、传感器与机器人本身的易用性是三股重要趋势。比如可视化技术的持续发展,可视化系统和模拟仿真结合,可以将机器人的运动流程事先在数字化平台上呈现,以便于工程师进一步调整。等到真正投产时,机器人系统的可靠性就更大。可视化系统和传感器结合在一起,则可以让机器人更加精确高效。“这样一来,我们就可以看到实时会发生什么,看到了发生什么之后,就可以快速作出决策。” Zvi Feuer说。

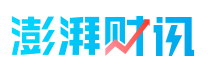
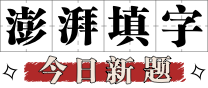
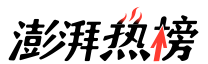
- 报料热线: 021-962866
- 报料邮箱: news@thepaper.cn
互联网新闻信息服务许可证:31120170006
增值电信业务经营许可证:沪B2-2017116
© 2014-2024 上海东方报业有限公司