- +1
超车,从工厂开始
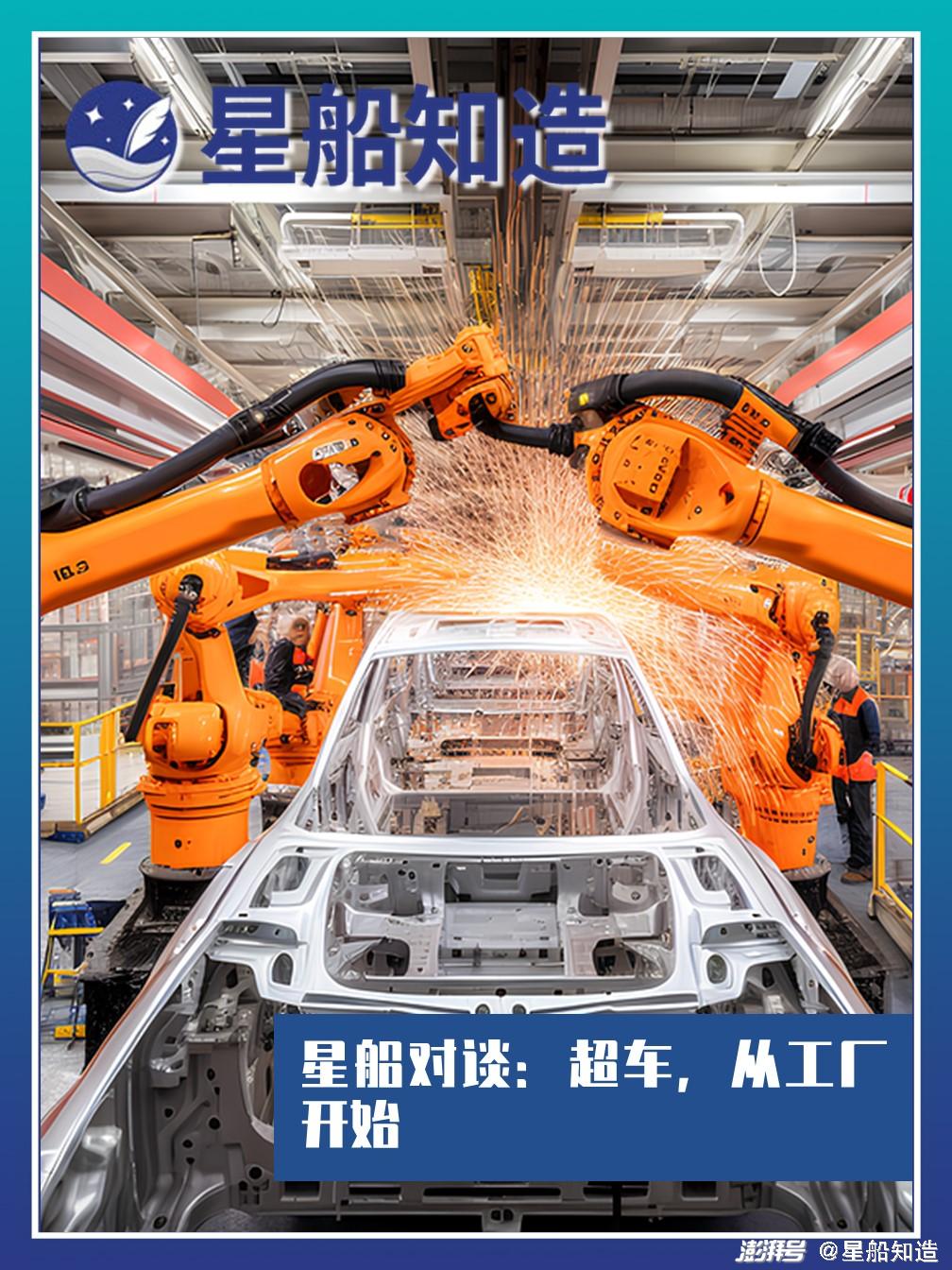
文、访谈整理| 星船知造
正文共计 :3732字
预计阅读时间 :5分钟
如何为产品撰写定义?
90年代,李书福说“汽车就是四个轮子加一个沙发”。二十多年后,小米入局造车,雷军说电动车“就是四个轮子加一部大号手机”。
如何描述产品的生产方式?
上世纪初,福特生产方式(Ford-ism) 被认为是划时代的创新。福特创建的世界上第一条汽车装配流水线,让汽车工业从此具备规模化产业的基础。
五十年后,丰田精益生产被认为是现代工业典范。更经济的小型轿车风靡全球。
今天,中国新能源汽车产销连续8年全球第一,软硬结合的数智化思考方式开始贯穿汽车的设计至生产。它同时重构了中国工厂的形状。
如何理解汽车生产环节的数智化?
有时候,它是一些人们熟悉的工具。2019年,吉林长春。
一汽集团董事长徐留平决定引入协同办公产品,钉钉。用以辅助疫情期间的员工管理。三年后,一汽内部新增了300多个数字应用。上至员工在线办公,下至车间机器故障报警——更多造车过程中的工序数据奔向云端。
有时候它通过机器人这一具体抓手。2022年,广东。
广汽丰通生产车间里,移动机器人识别出地面上的二维码,迈步朝着目标输送线和拆码盘机前进。
中国本土工业机器人正依托汽车零部件、整车制造行业所带来的巨大应用市场,快速崛起、不断进化,并不断被复制到其他行业。
汽车产业是我国最早布局自动化、智能化生产的制造业领域,主要可分为汽车零配件和汽车主机制造两大类。
其中,主机厂主要有四大工艺“冲压、焊装、涂装、总装”。四个车间的生产特点颇为不同。
焊接机器人、移动机器人、六轴工业机器人主要穿梭、伫立于冲压、焊装、涂装这三个车间。
相比之下,总装车间的自动化程度略低一些。玻璃、轮胎、座椅等多个零部件都需要在这里组装完成,操作工艺更为复杂。需要大量人工装配、机器辅助。
目前中国汽车主机制造仍存在相当多的痛点,据星船知造此前调研了解到,大致有——
物流端,一是成本较高,主要表现为存在重复劳动和非增值作业、物料库存占压大量资金等。
二是由于车型更新换代加速,导致物料切换频繁、供应链上下游信息不够畅通,导致生产物料浪费等。
三是管理难,主要体现在现场人员流动性大、库存数据零散导致缺料停线等。
生产端,存在施工周期长、生产过程不透明,异常响应增加管理成本,数据统计及分析困难等痛点。
在自动化向智能化转型升级的过程中,这些痛点要如何被逐个击破解决?
2023年,苏州。
在苏州举办的2023虎嗅工业AI大会上,星船知造创始人唐晓园和四位汽车业内专家:
理想汽车IT高级总监王会菲、广汽集团大圣科技副总经理吴大庆、联想创投董事总经理顾正斌、长城汽车IDC大数据AI领域负责人薄猛,共同探讨:
●中国汽车制造的数智化行进到哪一步了?
●头部车企都有哪些数字化转型成就?
Q1
星船知造唐晓园:
“自动化、数字化,智能化、数智化”,具体到整车制造的不同环节、不同车间,该怎么来理解这四化?聊聊对智能制造的看法。
长城汽车IDC大数据AI领域负责人薄猛:
四化里,相对最简单的是自动化。然后如何让设备实现准确判定,这里就需要考虑智能化。而让设备做出智能化决策依据的,是来源于我们现场实际业务的数据——也就是说,要实现设备的智能化,必须要先实现数字化。通过数字化管控来提高有效生产,以此来真正引导一个产品的自动化、智能化、数智化。
理想汽车IT高级总监王会菲:
从我的理解来看,大家容易把智能化简单的理解为更自动化。在我看来,自动化和数字化是智能化的基础,用通俗易懂的话来解释智能化,就是说它必须得有大脑,能够思考和判断,所以我们对智能工厂的要求就是要具备感知、规划、决策和执行的闭环能力。
智能制造的终极目标就是黑灯工厂,理想汽车一直致力于通过IT技术提高生产力,通过自研智能制造操作系统Li-MOS,以及AI研发和视觉应用等,让生产机器的机器更加智能,所以我们也在数字化、智能化等方面做了很多探索和创新。
联想创投董事总经理顾正斌:
在我看来,汽车四化其实做挺好的,其中生产环境的自动化程度可以继续提高,但是总体提升空间并不是很大。目前很大的提升空间是在于研发、试制等阶段,尤其是在小批量生产方面。比如一台新车型,我们最低恐怕要试制130台,有的车可能需要新车试制150台或200台。那能不能通过这四化来减少试制的数量呢?比如说只用80台或90台就完成验证,这个领域我觉得会有较大提升空间。
再就是车身材料的应用方面,业内对新材料的应用,总体上认为是趋势,中国车厂在新车型上使用新材料更加创新大胆;同时又心存顾忌。例如将原来的钢材,改成铝、改成铝镁等新材料,业内对于这些材料的量产制造工艺目前有顾虑的,尤其是新的连接工艺如铆接、焊接等等存在顾虑的。可能实验室中验证过了,但放在批量生产的时候还是会有所顾虑。
但我认为将来车身新材料的研发在全国甚至全球的汽车行业都会掀起新的浪潮。因为钢车身在欧洲国家、美国和日本已经研究很深了,所有的车型他们都很清楚,但是新材料,尤其是减重的新材料,中国企业与这些国家差距不大,未来的机会会更多一些。
广汽集团大圣科技副总经理吴大庆:
过去我去日本参观丰田的时候,觉得他们的整车制造已经很棒了。但这几年,我们广汽埃安的智能工厂的建设,让我非常自豪,我们现在在智能制造方面已经不比丰田差了。
不过在我来看,智能制造其实不是一定要打造黑灯工厂,并不是一定要围绕黑灯工厂来做。比如埃安智能生态工厂也是工信部授予的智能制造示范工厂,埃安工厂的智能制造更多是从用户的需求出发,更多考虑用户的个性化需求。是以满足用户需求来作为智能工厂的定位。
Q2
星船知造唐晓园:
这样看来,目前整车厂的智能化布局已经走在了前面,但相关供应链企业、或者研发端,是不是还有相当多的数据孤岛耸立?未来可能利用哪些技术或手段来打破这一现状,加快智能化的布局?
广汽集团大圣科技副总经理吴大庆:
我们现在更多思考的其实是如何把数字化更深入地运用起来。在这一方面,我们也有和客户一起研发汽车的经验,融合客户的需求和偏好数据来设计汽车,也实现了销量的增长。甚至说有一些功能在设计师看来并不那么好,但客户反应非常强烈,所以我想数字化的未来是如何把这些数据用好,如何实现数字化的迭代升级。
而要说进入智能化,确实还需要一定的时间。
长城汽车IDC大数据AI领域负责人薄猛:
对于这一问题长城汽车也在探索,我们认为技术是未来发展的基石。目前我们(工厂)在5G的基础上更进一步,已经通过了全国首个5.5G的验证。这一技术能够真正把隐私网络和现场的生产管理情况纳入数字化设备中,让5G网络真正成为工业型网络。
理想汽车IT高级总监王会菲:
智能化不是一蹴而就的,信息化和数字化是智能化非常重要的基础。具体到实施上,有两种做法:一种是单点突破,在一些工位或工段采用机械手、机器人等手段来提高生产效率,或者是叫做机器替人。
另外一种做法是通过全链路数字化和智能化,提高整体生产力,这也是理想汽车的实践和做法。我们在数字化进程中有两点实践经验和大家分享交流:
一是自研智能制造操作系统(Li-MOS)。我们坚持自研是因为传统的MES系统在智能化集成和应用方面有很多的局限和技术壁垒,包括技术架构局限、设备与设备之间的互联、设备与系统的互联以及端口技术的限制等等,自研智能制造操作系统让智能制造的扩展空间具备无限可能。
二是对物联网、大数据、云计算以及大模型等深度研究和应用,包括数据整合和集成能力都是非常重要的,有了智能化全链路的技术研发、整合和集成应用的能力,智能化才有可能真正落地,赋能业务和创造价值。
Q3
星船知造创始人唐晓园:
为什么零配件企业在自动化和智能化的升级布局上,远比不上整车厂?
联想创投董事总经理顾正斌:
首先是复杂度。零配件领域会比整车厂复杂得多。一些高价值领域,比如电池、电机的自动化程度是相对高的,还有一些零配件自动化的价值空间很低,目前就不一定有必要(升级)。
第二个是从产业链来看,零配件的自动化有时可以带动它的一级上下游也进行自动化,但要再影响二级、三级就不容易,再加上有的零配件是属于其他工业体系,行业跨度较大,也不容易被影响。
广汽集团大圣科技副总经理吴大庆:
我认为是由于过去合资品牌给我们设定了很多门槛,限制了国产零部件企业团队的自动化。随着我们自主品牌的崛起,我们需要给更多国产零配件厂商机会,这样的话零配件企业的数字化和智能化才能加快进程。
理想汽车IT高级总监王会菲:
零部件企业的业务类型、规模、生产工艺等跟整车厂有比较大的差异,自动化需求和必要性差别也很大。零部件企业作为一个商业体,在智能制造方面的投资和建设必须要考虑企业实际需求、生产工艺和投资回报,不能为了智能而智能,我认为企业智能化的投资建设既是企业的一个战略选择,也是一个商业行为。
更多汽车智造内容,请点击《星船知造》——
●车间里的焊接机器人 《中国:焊接未来》
●锂电车间的数智化走到哪一步 《为什么大厂云“进不了”这个制造业车间?》
●看不见的手《特斯拉隐秘的恐惧:中国新能源车爆发背后的50年棋局》
以上对话部分内容仅代表嘉宾个人意见
本文不构成任何投资建议
本文为澎湃号作者或机构在澎湃新闻上传并发布,仅代表该作者或机构观点,不代表澎湃新闻的观点或立场,澎湃新闻仅提供信息发布平台。申请澎湃号请用电脑访问http://renzheng.thepaper.cn。

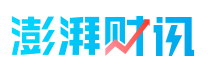
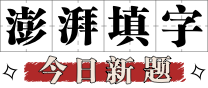
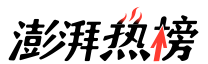
- 报料热线: 021-962866
- 报料邮箱: news@thepaper.cn
互联网新闻信息服务许可证:31120170006
增值电信业务经营许可证:沪B2-2017116
© 2014-2024 上海东方报业有限公司