- +1
【复材资讯】复合材料薄壁加筋结构优化设计与增材制造综述
【摘要】
复合材料薄壁加筋结构因具有轻质量、高强度、耐腐蚀、抗疲劳等优点,逐渐被用于航空航天、舰船邮轮、特种工程等高端装备制造。主要从薄壁加筋先进结构设计方法、复合材料增材制造工艺及复合材料薄壁加筋结构在航空航天领域的应用 3 个方面对当前研究进展和应用情况进行综述。针对加筋结构优化设计,概述了参数化方法、形状优化方法、拓扑优化方法及其他新型设计方法的基本原理;围绕复合材料增材制造技术,讨论了具体制造工艺的发展现状,以及其纤维铺放 / 打印路径规划方法;并梳理了航空航天高端装备领域中典型的复合材料薄壁加筋结构应用;最后总结了复合材料薄壁加筋结构 – 工艺协同设计的发展趋势及面临的关键挑战。
【作者】
任慧琳,熊 异
(南方科技大学,深圳 518055)
正文
航天运输系统、深空探测器和战略武器等高端装备领域的发展服务于国家重大战略需求,是国家综合科技水平和工业制造能力的重要标志。大运力、长寿命、远射程等装备需求促进关键结构件向着轻量化、高性能方向发展 [1]。复合材料薄壁结构作为轻质、高强设计的典型代表,被广泛用于航空航天、舰船邮轮、特种工程等重要领域。近年来,复合材料增材制造工艺的迅猛发展使得具有复杂设计的复合材料薄壁加筋结构制造成为可能。如何充分挖掘设计空间以提高结构件性能并充分考虑制造工艺等约束,对设计人员提出了更高挑战。
在上述背景下,本文围绕薄壁加筋结构设计和复合材料增材制造工艺对国内外研究进展进行分析,积极探索结构 – 工艺 – 性能一体化设计方法,以推动增材制造技术在复合材料薄壁加筋结构设计制造中的应用,实现下一代高性能复合材料薄壁加筋结构的设计制造。
01 薄壁加筋结构设计方法
为满足高端装备领域高性能、轻量化需求,关键结构件的设计常采用薄壁加筋结构,如飞机蒙皮 / 壁板、火箭压力储罐、飞行器密封舱等。传统的层合板构件逐渐向薄壁加筋、多级加筋 [2–3]、结构 – 工艺协同优化等方向发展,衍生出了一系列加强筋结构设计方法。
1.1 参数化方法
参数化方法是一种快速设计方法,可以通过对参考路径进行镜像和偏置得到全局加强筋布置。根据参考路径的角度变化,可以将参数化方法分为固定角度、线性变角度、非线性变角度等类型。固定角度加强筋设计中,加强筋角度不随空间位置变化,即常见的直筋布局,如图 1(a)所示。随着纤维自动铺放技术的发展,制造具有变化曲率的加强筋成为可能,其设计方法也逐渐发展。在参数化方法中,通过定义和调整少数设计变量,可以实现整个区域内曲筋设计。根据设计域内加强筋角度变化特性,可分为线性变角度及非线性变角度加强筋设计。图 1 (b)是线性变角度加强筋设计示意图,筋条角度φ (x)随横坐标 x 线性变化,具体数值由式(1)中的角度 T1、T2 及偏置距离 β 决定 [4],其中 L 为平板沿 x 轴方向长度。非线性变角度曲筋设计是在线性变角度设计方法的基础上,通过引入 M×N 个控制点,实现更灵活的曲筋布置,如图 1 (c)所示 [5](其中,a 和 b 分别表示设计平板的长和宽,Tmn 表示(xm,yn)位置处控制点的加强筋角度)。基于非线性变角度曲筋设计方法,曲筋角度分布满足式(2)定义。
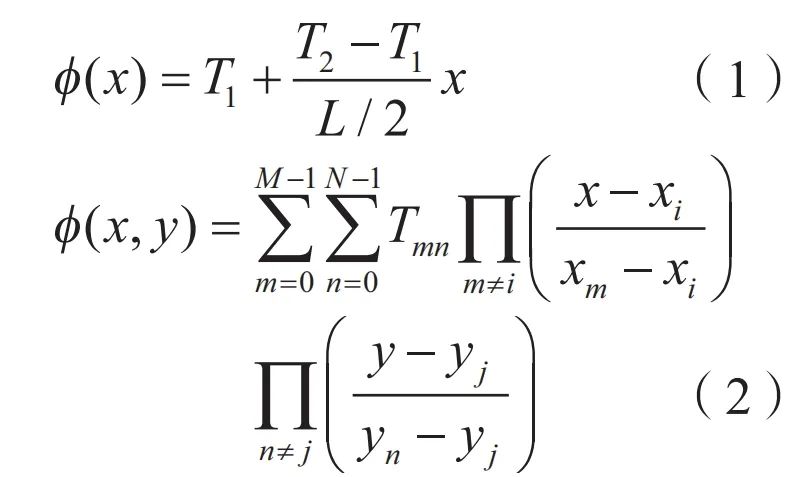
式中,φ(x,y)表示任意位置(x,y)处的曲筋角度;(xi,yi)和(xm,yn)分别表示参考点的 x–y 坐标。对于可展曲面,如圆柱、圆锥结构,常利用测地线路径作为加强筋参考路径,如图1(d)所示 [6](其中,φ(x)为筋条角度;x、y、z 分别表示圆锥上任一点的笛卡尔坐标;r 为不同高度处的圆锥半径;α 和 θ 分别表示锥角和周向曲面坐标)。这是因为在笛卡尔空间中,测地线路径是连接三维曲面上两点之间的最短路径 [7],也称作自然路径。由于测地线上的曲率变化最小,在承受外界载荷时,承力路径上曲率突变造成的应力集中现象减少,加强筋路径的拉伸和压缩应力也最小;同时,测地路径在曲面上的连续性和小曲率特性,减少了曲筋制造缺陷,从而达到最优的加强效果。测地线的求解取决于曲面的几何形状,常采用解析方法、数值方法及优化方法进行求解,MATLAB 等商业软件中也提供了相应工具箱。
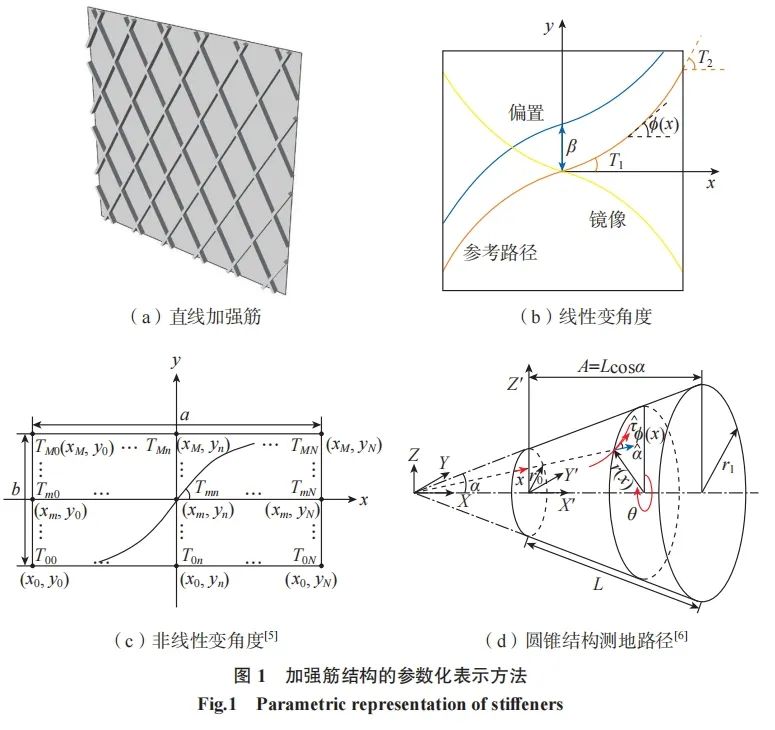
上述参数化方法通过凝聚设计变量,能够快速实现整个设计域内的曲筋复杂分布。这种基于简化的加强筋设计方法常与优化算法相结合,以高效寻找满足屈曲、抗弯或动态载荷等不同工况下的最优设计变量。这种基于简化的加强筋设计方法具有广泛的应用前景,为实现复杂结构的快速设计提供了新思路。
1.2 形状优化方法
加强筋设计中的形状优化方法是指在固定拓扑结构下寻找满足约束条件的加强筋边界形状 [8]。作为形状优化前提条件,需要建立加强筋形状数学模型,包括位置分布和几何曲率 [9–10],如图 2 所示 [11]。对于这种加筋薄壳结构,设计域 Ω 包含薄壳和加强筋的侧面 S、横截面 A 及其变化 dA、dAS,设计变量为加强筋处的速度矢量 V。这种复杂几何特征通常采用离散或者微分的方法进行求解,需要多次迭代,导致计算量较大。Liu 等 [11] 提出一种无参数形状优化方法,通过将固定体积特征值最大化问题及固定特征值体积最小化问题在连续空间内进行表征,实现无参数化和非离散化状态下的形状优化。
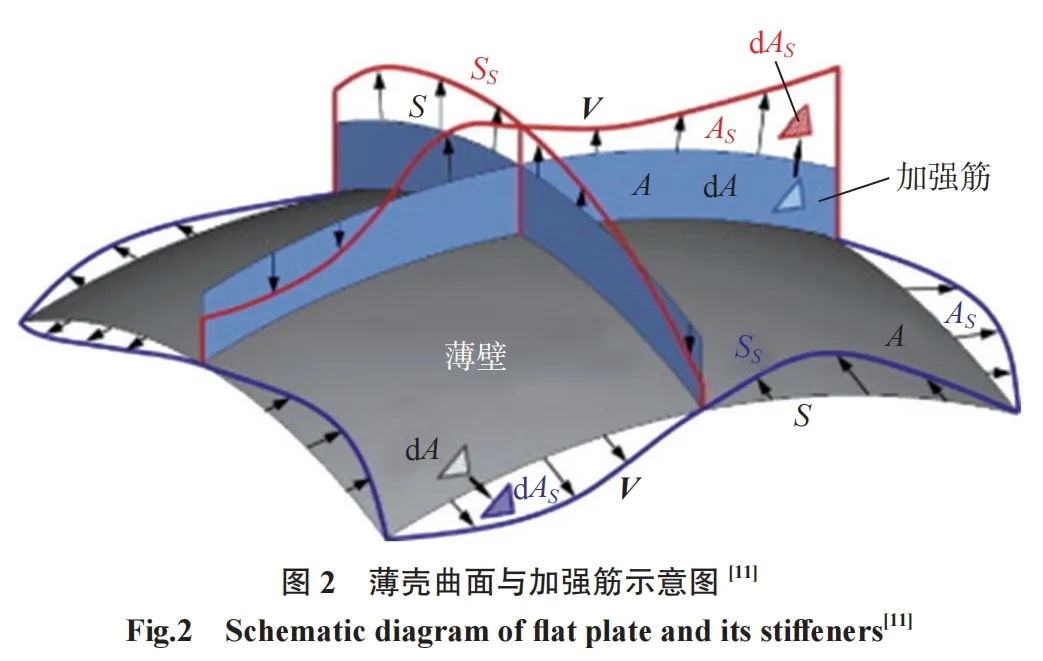
随着设计能力提高,几何形状复杂的薄壁加筋结构对网格细化、数值精度和计算成本提出了严苛的要求。Hughes 等 [12] 首先引入了基于非均匀有理 B 样条(Non-uniform rationalB-splines,NURBS)基函数的等几何分析(Isogeometric analysis,IGA)方法,有效解决有限元网格计算中成本高、耗时长、几何误差大等问题。同时,IGA 方法能够实现计算机辅助设计(CAD)和计算机辅助工程(CAE)步骤之间的无缝衔接,有利于设计过程自动化。Hao 等 [13] 比较了 IGA 方法和传统有限元仿真方法,如图 3 所示,将 IGA 方法应用到加强筋设计领域,将描述加强筋几何形状的形状函数作为基函数,并基于 NURBS 投影和插值算法,实现了壳体与筋之间的自适应强耦合。
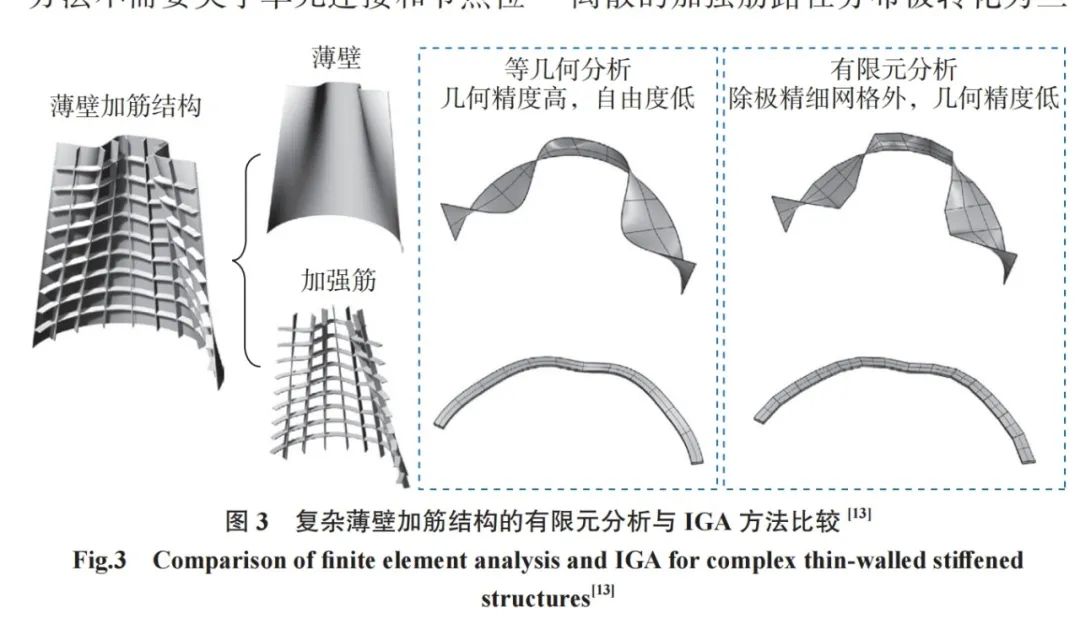
1.3 拓扑优化方法
拓扑优化 [14–15] 作为一种先进结构设计方法,能够根据给定负载、约束和性能指标,在设计域内获得最佳材料分布。将拓扑优化这种先进设计方法与增材制造等工艺相结合,能够充分挖掘结构 – 工艺协同设计的潜力。值得注意的是,基于各向异性材料 / 纤维路径分布的拓扑优化算法近年来获得较大发展 [16–19]。
基于拓扑优化的薄壁加筋结构设计方法,即通过优化设计域内均质材料的分布得到满足设计目标的加筋拓扑构型。在拓扑优化中,微观尺度上计算每个单元的刚度系数,并在宏观尺度上针对特定的设计目标进行优化,获得具有抗屈曲、抗弯曲或良好动态特性的薄壁加筋结构设计,如图 4 所示 [20](其中,t 为平板厚度;h 为加强筋高度;Ke(h)为加强筋的单元刚度矩阵;Ke(t)为平板的单元刚度矩阵)。
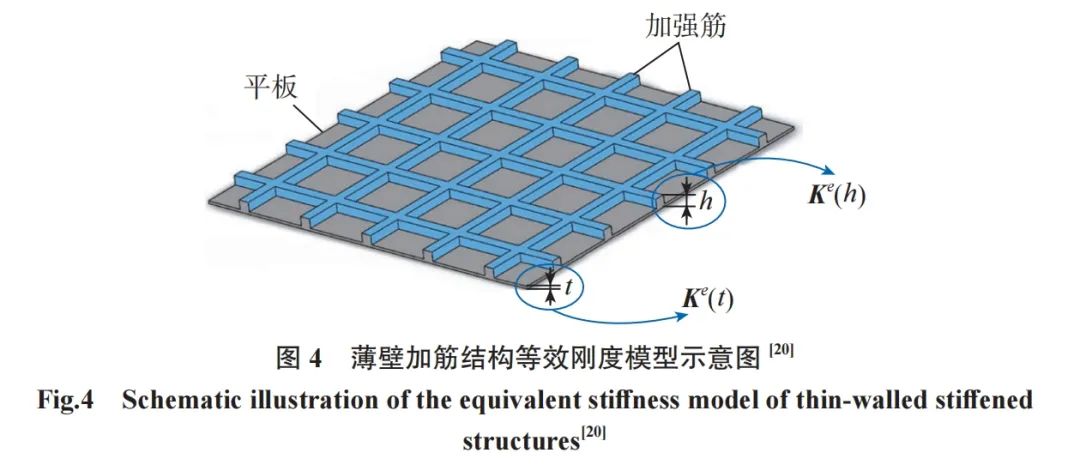
近年来,基于连续介质拓扑优化方法的薄壁加筋、多级加筋结构 [21] 优化设计成为研究的热点之一。常见的方法包括经典的均质化方法 [22]、变密度法 [23]、水平集方法 [24] 和特征映射方法 [25] 等。此外,针对不同应用领域和具体工程问题,还有一些创新性的拓扑优化方法被提出和应用。Wei等 [26] 提出了用于桁架结构优化的刚度扩散法(Stiffness spreading method,SSM),桁架结构被嵌入到一个弱约束连续体网格中,杆单元可以在设计域中自由移动,且具有解析敏度;该方法同时实现了桁架结构的尺寸、形状和拓扑设计优化,图 5 展示了不同迭代次数(n)时的桁架结构设计结果。与传统的拓扑优化方法不同,该方法不需要关于单元连接和节点位置的先验知识,对于加强筋结构设计同样具有参考意义。
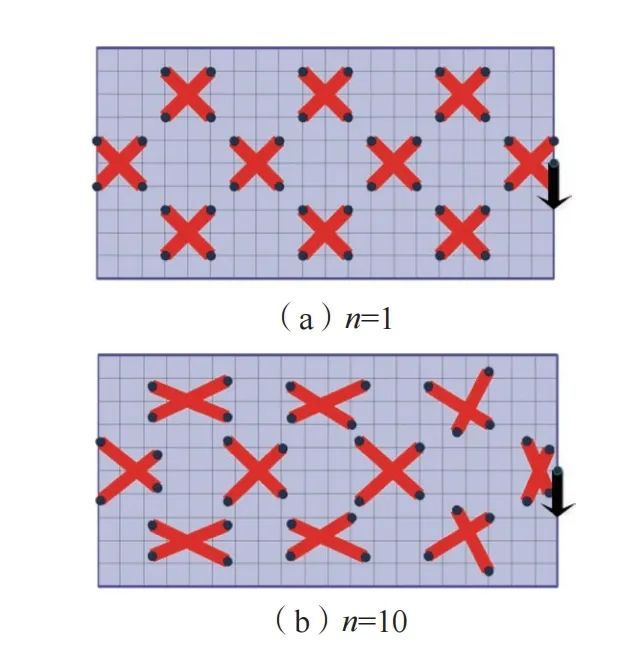
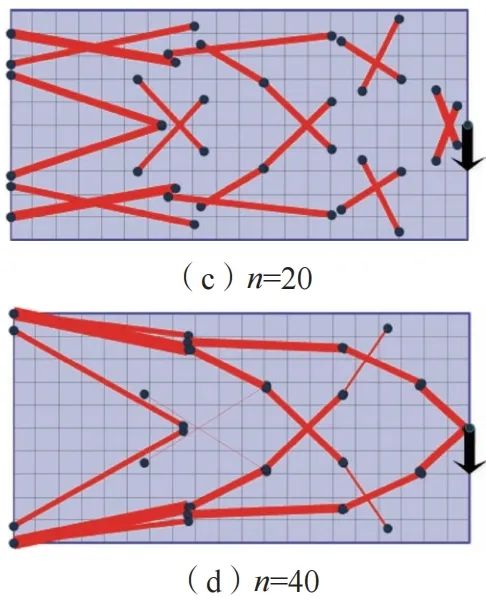
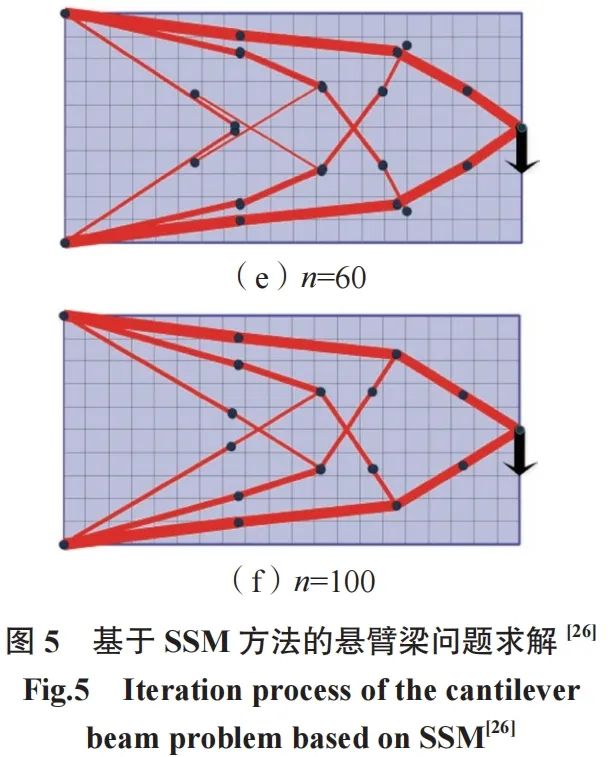
1.4 新型设计方法
然而,在加强筋布局设计中存在两个关键问题:(1)初始曲筋信息未知;(2)加强筋交叉点的网格形状多变,形状优化和拓扑优化都无法直接解决这些问题 [27]。为了处理这些问题,Wang 等 [27] 提出了基于流线函数的加强筋设计方法,如图 6 所示,首先,基于流线函数给出了流线型加强筋的定义,并通过全局 / 局部均质化方法和敏度分析 [28],实现了多尺度建模的流线型曲筋设计;使用流线函数描述加强筋路径与水平集方法类似:连续分布的流线函数值形成每个加强筋簇的三维水平集曲面,该曲面在二维平面的投影就是曲线加强筋路径。图 6(a)和(b)展示了固定节点上的不同流线函数值,其对应的加强筋路径如图 6(c)和(d)所示。通过这种方法,二维设计域中离散的加强筋路径分布被转化为三维水平集曲面上的连续流函数值分布。该方法无明显的尺度效应,适用于分布较密的加强筋设计。
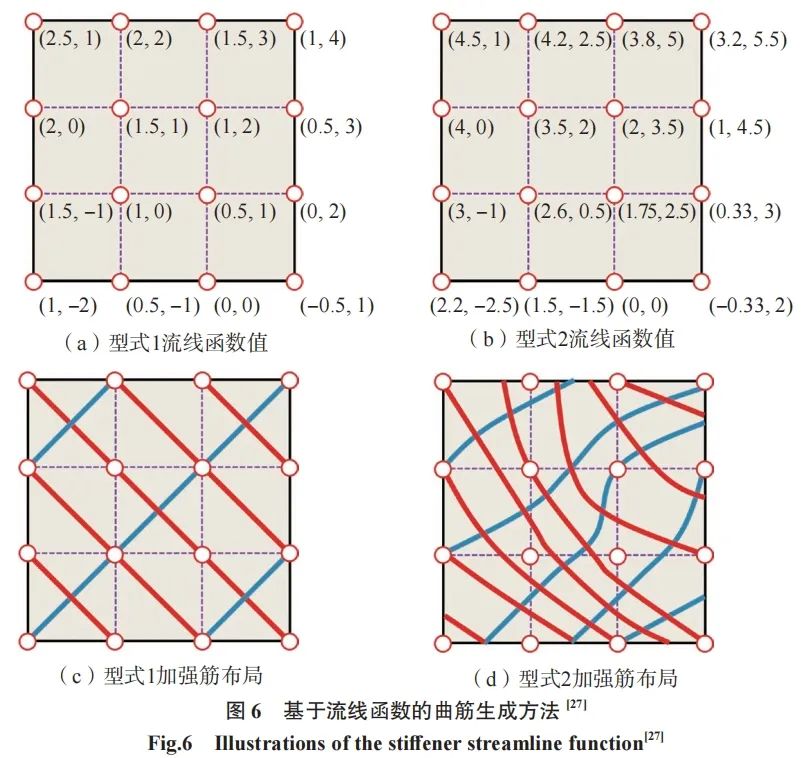
对于优化问题中存在的大量迭代步,有学者利用这一过程曲筋形式 – 结构响应的大量数据,利用数据驱动的方法进行薄壁加筋结构设计。Wang 等 [29] 通过提取影响结构性能的主成分,实现了基于主成分分析(Principal component analysis,PCA)的数据驱动方法。张坤鹏等 [30] 将加强筋结构特征参数转化为 RGB 图像,并利用卷积神经网络搭建基于图像识别的深度学习网络模型,实现数据驱动下的结构优化设计。
同时,自然界中存在着大量天然加筋结构,如植物叶脉、鸟类翅脉等。这些曲筋的结构形式和生长方法为工程结构的加强筋设计提供了设计灵感 [31–32]。模拟树生长和分支规律,Dong 等 [33] 提出了一种生成式曲筋优化方法,根据加强筋分支延伸的效果自适应选择分支的最佳生长方向,并通过控制体积增长速度实现整体结构体积控制,如图 7 所示。
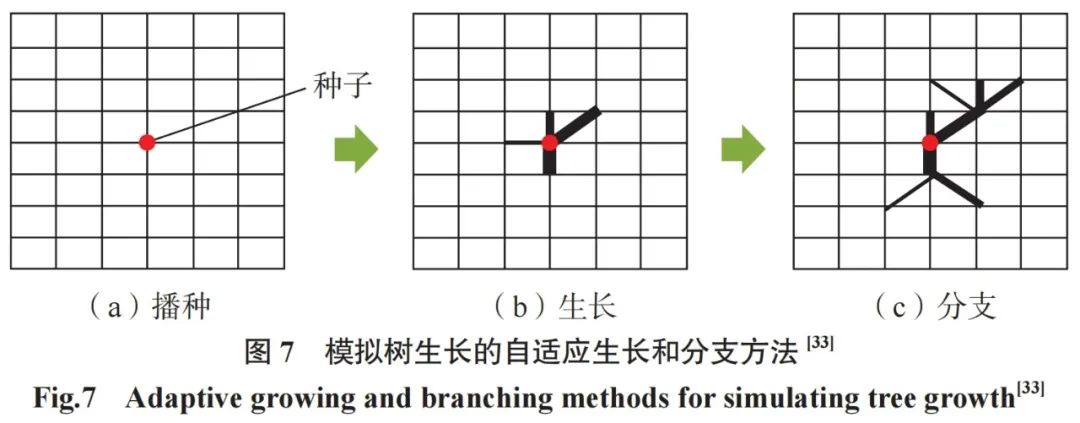
02 复合材料增材制造工艺
薄壁加筋结构通常由薄壳本体和加强筋构成,为了制造这种结构,需要高精度、高灵活性的制造技术,以确保结构的强度和稳定性。传统的复合材料薄壁加筋结构件制造方法有手糊成型法、树脂传递模塑等。相比于这些传统制造工艺,基于增材制造的新型复材制造方法,如纤维缠绕技术、自动铺放技术、3D 打印技术等,不需要模具和繁多工序,能够实现复杂、大型、多级构件的一体化成型。利用增材制造技术制造薄壁加筋结构,可以快速、精确、灵活地实现复杂曲筋薄壁结构的制造成型,提高生产效率和质量。同时,利用增材制造技术还可以减少材料浪费,降低生产成本。
2.1 纤维缠绕技术
纤维缠绕技术(Filament winding,FW)是最早开发的复合材料自动化成型技术 [34–35],易于实现机械化和自动化,便于大批量生产,尤其适用于圆柱、圆锥等回转类构件制造,其工艺示意图如图 8 所示。纤维缠绕工艺可以实现将预先张紧的纤维以预定线型连续缠绕在芯模上,随后在室温或加热条件下固化,从而形成具有一定形状的纤维制品 [36]。纤维缠绕技术可以控制纤维的方向、角度及厚度,进而根据结构件承载需求设计不同的纤维缠绕方案,以实现高强度、高刚度、轻质的复合材料结构件。这种工艺技术在高压储罐、压力管道、发动机壳体等领域得到了广泛应用。
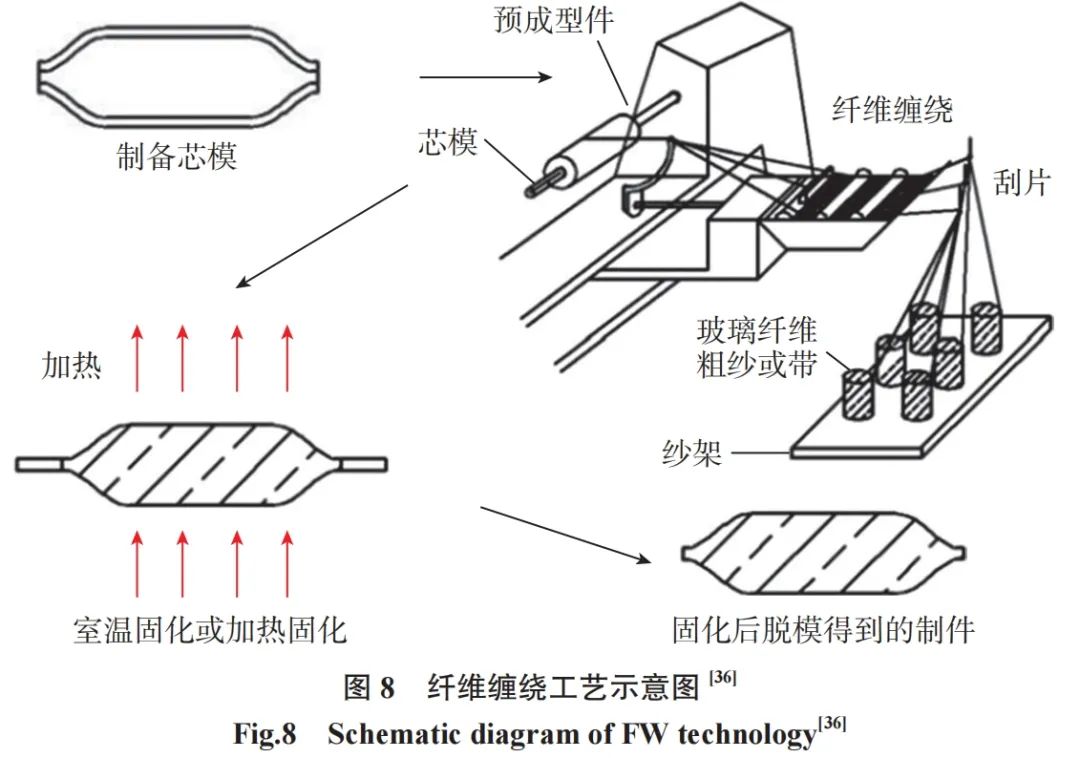
利用纤维缠绕技术制造加强筋主要由芯模结构实现。根据种类可以将模具分为凹槽和销钉两类。凹槽模具用于将纤维定位在凹槽内布,如图 9(a)所示 [37]。常用于制作出具有规则几何形状的加强筋,如环形、三角形、Kagome 形等。与凹槽模具相比,销钉模具更为灵活,可以制作出更为复杂的加强筋形状。销钉模具通常由多个销钉组成,这些销钉可以在不同的位置和角度上固定纤维,从而实现不同形状的加强筋制作,如图 9(b)所示 [38]。
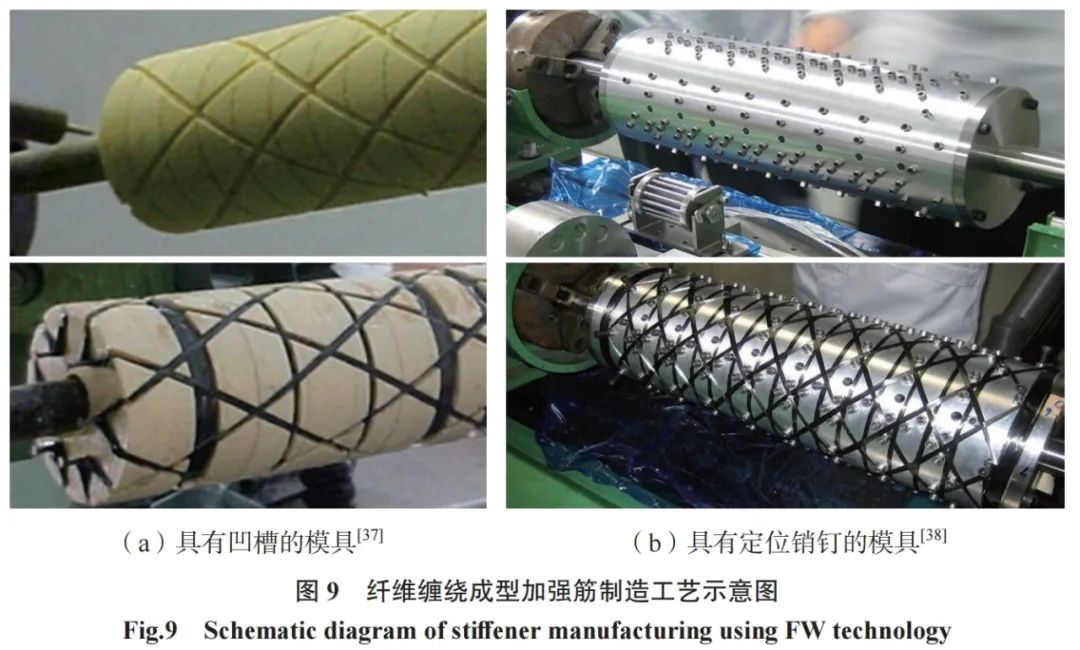
纤维缠绕技术作为一种重要的复合材料自动化成型技术,在制件结构 – 工艺 – 性能一体化设计制造过程中存在一定的局限性,主要体现在结构件的形状限制方面。目前纤维缠绕技术的制品主要为具有凸曲率属性的回转体,例如圆柱体、球体等,对于非回转体或凹曲线结构件的制造能力较差。此外,纤维缠绕技术本身还面临着一些技术上的不足和挑战,比如,纤维缠绕过程中涉及多坐标运动控制 [39]、精密张力控制、过程工艺参数优化、缺陷在线监测技术等。
2.2 纤维自动铺放技术
纤维自动铺放技术(Automatedfiber placement,AFP)是一种高效率、高质量、高技术成熟度的增材制造工艺,相比于纤维缠绕技术,其制造能力更加灵活和多样化,可以制造更为复杂的形状和曲面结构,且不受制件轴对称限制。因此,纤维自动铺放技术广泛应用于航空航天领域的大型飞机、运载火箭等薄壁加筋结构件的设计和制造中 [40]。
纤维自动铺放技术采用机械臂或其他形式的自动化系统,将纤维束或纤维预浸带自动铺设在模具或基材的指定位置并原位固化,形成具有特定物理机械性能的复合材料结构。根据台架系统类型,纤维自动铺放技术可以分为龙门式、卧式和机械手臂式等不同类型 [41],如图 10 所示 [42–44]。铺丝头作为自动铺放技术的核心机构,具有送带、预紧、切带、加热、滚压等多种功能,以适应加工过程中各项铺放工作,如图 11 所示 [41,45]。铺丝头的高精度、高速度、长寿命、易于维护等特点对自动铺放技术的性能和工作效率具有重要影响。新型的铺丝头技术包括基于机器视觉和人工智能技术的自适应控制方法 [46] 和基于光纤传感和精密控制技术的高精度铺丝头 [47] 等,这些技术可以提高铺放质量和生产效率。
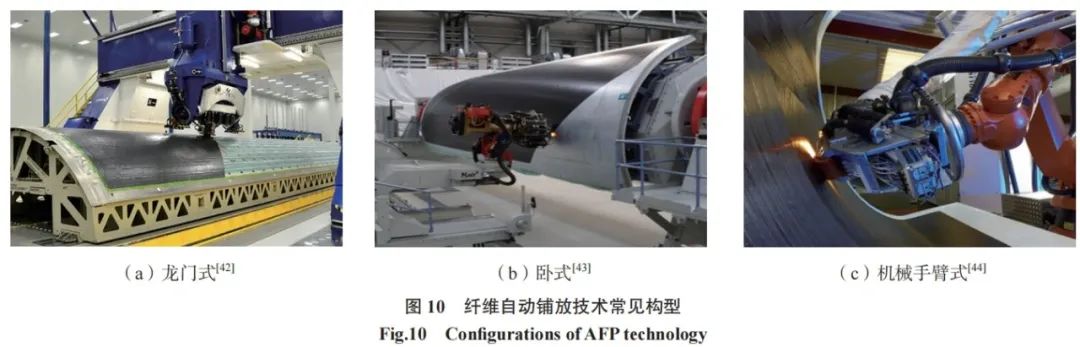
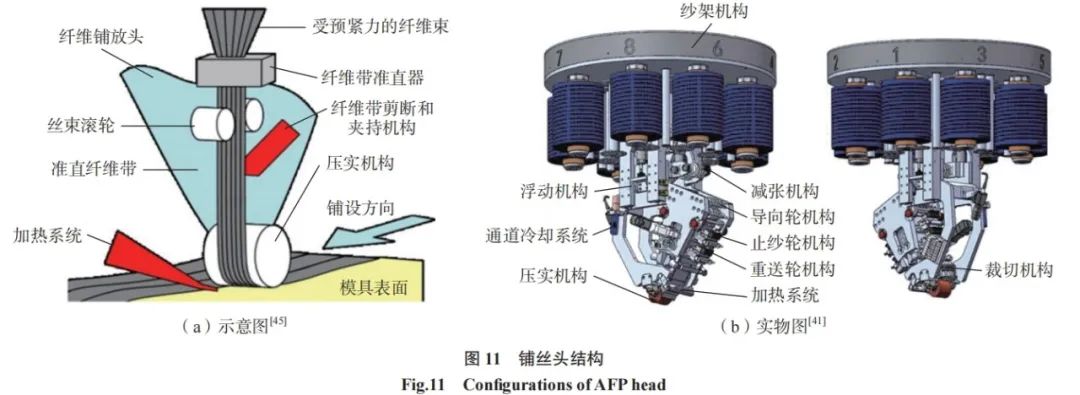
自动铺放技术在筋 – 壳一体成型方面的应用,主要优势在于加工灵活度使其能够在加工曲面的任意区域铺设加强筋,无须预先设计的凹槽模具或销钉定位。在此基础上,铺丝头的加热、滚压功能能够强化加强筋与薄壳之前的结合。为了进一步提高加强筋与薄壳之间的结合强度,在一体化加工成型时,可采用加强筋内嵌 [48] 的方法进行一体化制造,将加强筋包裹在蒙皮内部,有效减少加强筋脱离现象,提高结构承载能力。此外,针对加强筋交叉节点处的材料堆叠和局部缺陷,常采用节点偏置 [49]的方法提高节点处的表面形貌和力学性能。
尽管纤维自动铺放技术具有众多优点,但由于其使用特定的材料和工艺,其在实际制造中还存在一些限制和挑战,以工艺规划软件为例,为了实现高精度的自动铺放,工艺规划软件需要具备模型分析、切片规划、路径生成等多种功能。在模型分析方面,切片软件需要对 3D 模型进行分析,检测其中难加工特征,如重叠区域、内部空洞等,并能够自动处理这些问题。在切片规划方面,切片软件需要将 3D 模型切割为多层 2D 图形,并对每一层进行规划,确定铺放路径和铺放顺序等,减少纤维带重叠、空隙等制造缺陷。在路径生成方面,切片软件需要生成高效、准确的路径,并考虑到纤维带的材料属性、纤维方向、厚度等因素,以确保铺放过程中的质量和效率。
2.3 3D 打印技术
3D 打印是一种将材料堆叠实现复杂结构“生长”成形的新型制造工艺,具有快速定制和高度灵活的特点,能够实现复杂结构件的加工制造,大幅缩短零件生产周期,提高生产材料利用率,降低生产成本。对于纤维增强复合材料,沿纤维轴方向相对其法向表现出很高的强度,因此增强的复合材料具有各向异性的宏观力学性能。相比于传统的铺丝、铺带制造工艺,3D 打印技术具有更高的精度和灵活性,可以通过合理的路径规划,按照设计需求在零件的局部区域内打印纤维,从而实现定制化的力学性能分布。图 12[50–52] 展示了 3 种常见的短纤维增强复合材料 3D 打印技术。尽管面向短纤维增强复合材料的增材制造技术变体较多,但其对零件力学性能的改善效果有限。因此,深入研究 3D 打印技术在连续纤维增强复合材料制造中的应用和发展,具有重要的科学意义和实际价值。
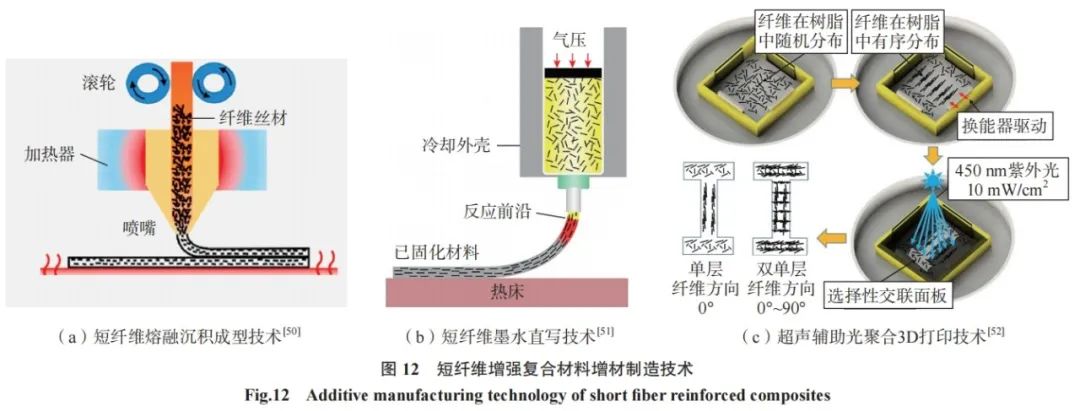
部分学者和企业在传统树脂熔融沉积成型技术的基础上进行了改进,优化了送丝机构、喷嘴,并增加了剪丝机构等,发展出了具有连续纤维打印能力的熔融沉积成型技术(Fused deposition modeling,FDM),从而显著提高了零件的力学性能。和多材料 FDM 技术类似,挤出机构配备有两套送丝机构和进料口,分别控制树脂和纤维进给量,如图 13[53] 和图 14[54] 所示。连续纤维打印技术与传统树脂打印技术不同,对喷嘴的耐磨性和腔道内流动性提出了更高的设计要求 [55]。目前,已经有一些较为成熟的连续纤维增强复合材料 3D 打印机供应商,例如美国的 Markforged、Arevo、Continuous Composites、Impossible Objects 公司和俄罗斯的Anisoprint 公司等。这些公司在该领域中不断进行创新研究和技术革新,推动了连续纤维增强复合材料 3D 打印技术的发展。
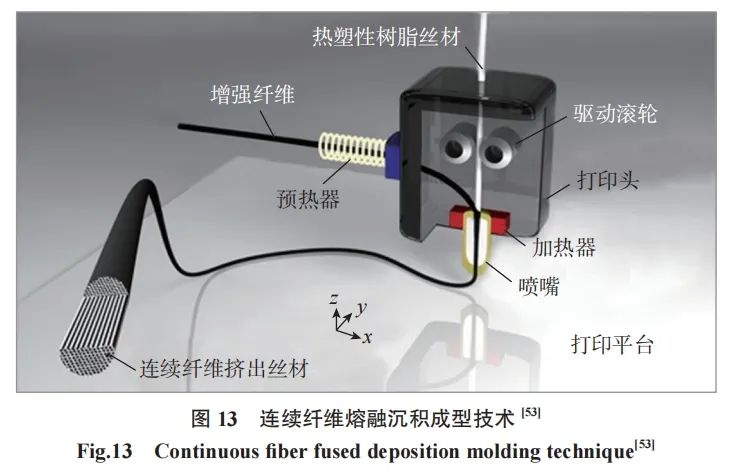
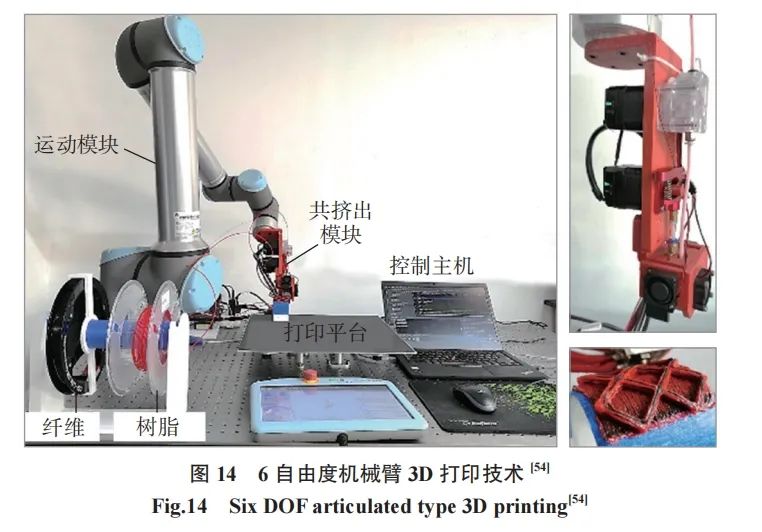
目前,针对连续纤维 3D 打印的切片软件较少,主要为上述连续纤维FDM 打印机配套软件,以 Eiger® 和Aura® 为代表,其打印机具有纤维剪断装置,可以根据实际打印结构自动生成纤维分布、路径和含量,实现几何形状内部的纤维填充。但这些商业软件中关于纤维路径设计的功能有限,仅提供图案填充方法选项和基本控制参数,通常会导致纤维无效 /低效增强、纤维局部不均匀/不对称,以及纤维分布碎片化等缺陷 [56–58]。
在当前的增材制造技术中,连续纤维熔融沉积成型技术已经能够实现夹芯结构的设计制造。图 15[59] 展示了不同夹芯型式的纤维路径设计。夹芯结构具有类似于薄壁加筋结构的特征,因此其工艺设计包括筋壳一体打印、加强筋(内芯)形式、纤维路径规划等同样是需要考虑的内容。
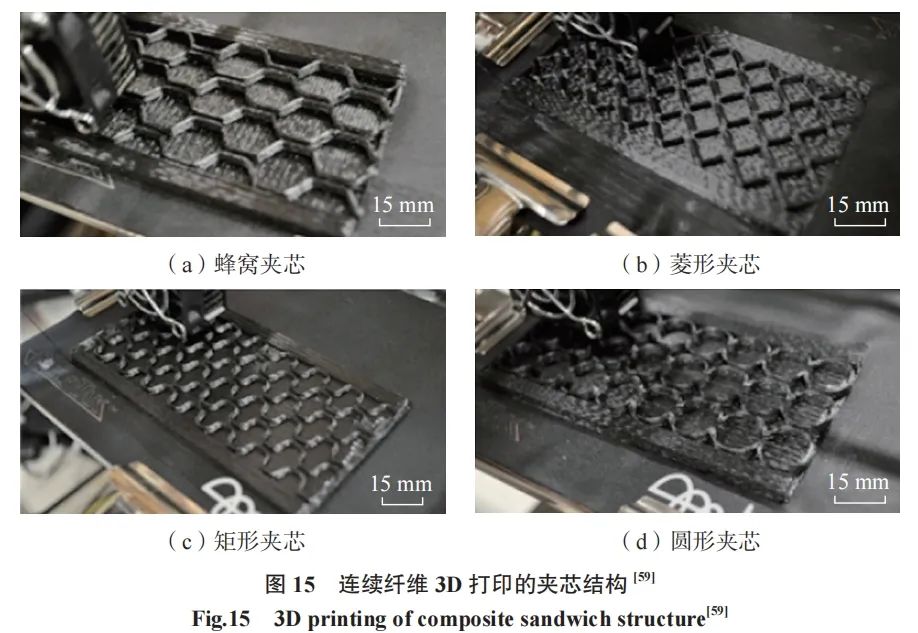
随着增材制造技术的发展,传统平面分层打印技术的局限性日益显现。尤其对于连续纤维增强复合材料,其力学性能受到纤维取向的影响,而平面分层打印技术只能在二维平面内排布纤维,无法沿堆积方向进行优化布置,限制零件空间内的力学性能。因此,开发出基于多自由度机械臂的曲面纤维 3D 打印技术是亟须解决的问题。如图 14 所示,这种技术可以实现纤维在三维曲面内沿任意运动轨迹进行 3D 打印制造,从而获得具有空间力学性能的复合材料薄壁加筋结构。目前,该技术仍处于研究阶段,相关研究者正在探索空间曲面纤维的喷嘴结构、路径设计、控制算法等关键技术,以进一步提高制造精度和产品质量。未来,曲面纤维 3D 打印技术有望在航空航天、汽车、船舶等领域中得到广泛应用。
同时,基于上述纤维增强复合材料增材制造技术,一些性能驱动的纤维路径规划方法呈现出从粗糙到精确、从平面到曲面、从时序设计到并行设计的发展趋势,如图 16 所示 [17,60–62]。这些纤维路径规划方法提供了加强筋设计新思路,与现有薄壁加筋结构设计相比,突破了规则设计域、初始加强筋构型、不同优化目标解析敏度难以计算等限制,适用于不规则、复杂、三维的薄壁加筋结构设计。此外,这些规划方法与拓扑优化这种先进结构优化方法的结合实现了筋 –壳一体化设计,尤其适合成型过程的筋 – 壳一体化增材制造。这些进展为加强复合材料薄壁结构的设计制造提供了新的思路和方法。
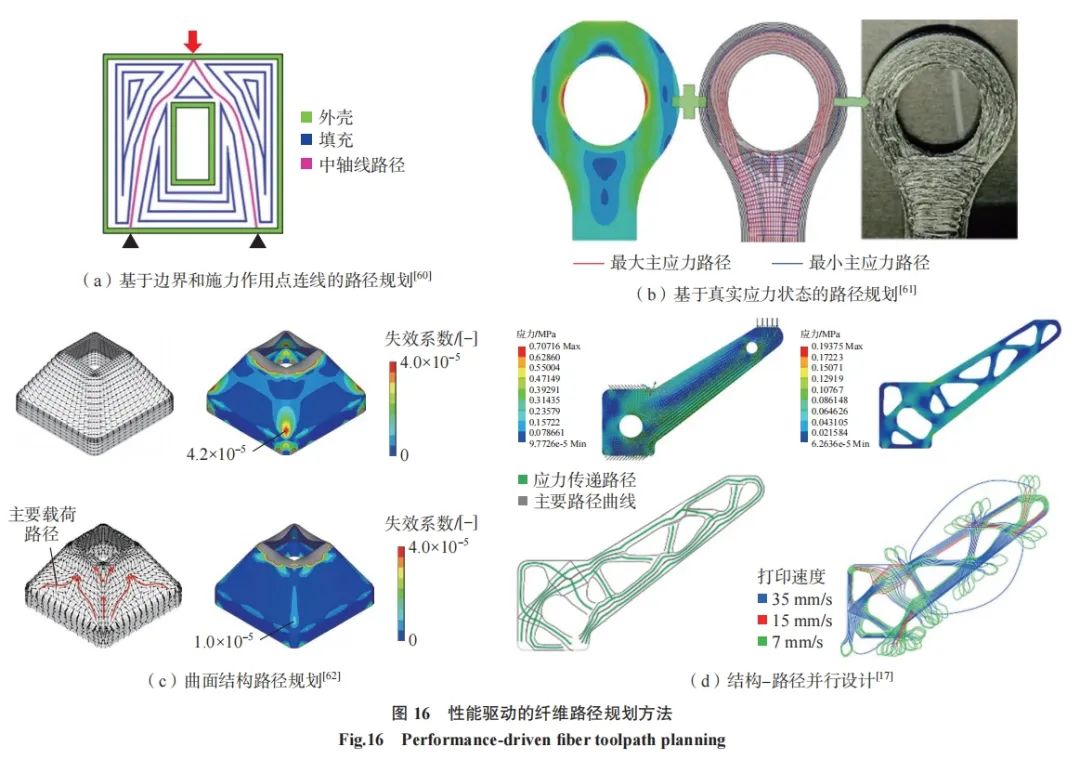
2.4 机遇与挑战
尽管纤维增强复合材料增材制造在薄壁加筋结构上具有广阔前景,但离大规模应用还有一定距离,主要受限于制造效率和工艺质量。目前,复合材料增材制造技术发展主要围绕缩短生产周期和提升产品性能两个方面,具体有以下发展趋势。
(1)先进材料的应用。选择具有更好力学性能的基体材料,如聚醚醚酮(PEEK)[63–64] 等高性能工程塑料 [65],能够提高复合材料整体性能。同时,采用新型的纤维材料,如碳化硅陶瓷纤维 [66] 等也有望进一步提高复合材料的高温耐受性和韧性。
(2)多种工艺相结合。探索多种工艺协同,如纤维缠绕、自动铺放、3D 打印等工艺之间的协同,如图 17所示 [67],通过纤维自动铺放技术与3D 打印技术相结合,实现大尺寸结构件快速成型与小范围内的材料填充、纤维加密与性能提升,以提高成品结构的整体性能和制造效率。同时,与激光辅助、超声融合等成型技术结合,能够提升纤维固化效率,实现原位铺放成型。
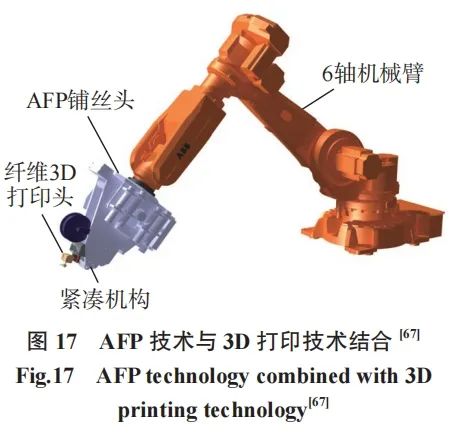
(3)路径规划与后处理软件发展。在结构设计同时进行纤维路径规划,能够实现结构和工艺的协同优化,以提高结构最终性能。目前,已有部分国外商业软件能够实现针对自动铺放技术的 CAD/CAM 环境集成,但针对设计和制造的性能评估还需要进一步提高,同时,国内自主产权的相关软件也需要加强研发。
(4)多机、多工序协同。多机协同以拓展工作范围、消除作业死区、提高生产效率,最终实现大尺寸结构件的快速成型。然而,多机组之间的运动精度控制是实现有效协同的关键技术手段,如图 18 所示 [68]。同时,多工序协同能够缩短工序间运转周期,降低设备空闲率,提高车间整体生产效率。为了实现多机、多工序的协同制造,还需要进一步研究优化算法、传感器网络、数据处理技术等方面的关键技术。
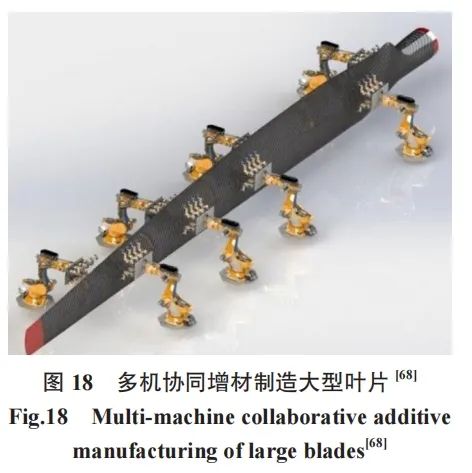
(5)在线检测技术。由于复合材料工艺缺陷存在多尺度的不确定性 [69],需要采用高精度的在线检测技术来实现缺陷的实时监测和控制。为了解决这些问题,当前正在研究和发展一些新的在线检测技术,例如基于红外成像的缺陷检测技术、基于声发射的损伤检测技术 [70]、基于纳米材料的传感器技术等。这些新技术能够更加精准地检测复合材料中的缺陷,并且具有更高的灵敏度和分辨率。
03 复合材料薄壁加筋结构在航空航天领域的应用
与金属增材制造发展规律类似,复合材料增材制造正在延伸到更多样化的领域,尤其是复合材料具有轻质、高强、耐腐蚀等优异性能,已成为航空航天领域的重要材料。复合材料用量也成为评价大飞机设计制造先进性的关键指标 [71],如波音 787复合材料用量达 50%,A350XWB 复合材料用量为 52%[35]。图 19[72] 展示了国产大飞机 C919 的复合材料使用情况,在这些由复合材料制造的零件中,包含大尺寸的薄壁加筋结构、夹芯结构、变曲率截面等复杂结构,增加了传统复材工艺的制造难度。而复合材料增材制造技术提供的灵活性与大尺寸制造能力为这些复杂承载结构件制造提供了新的选择。
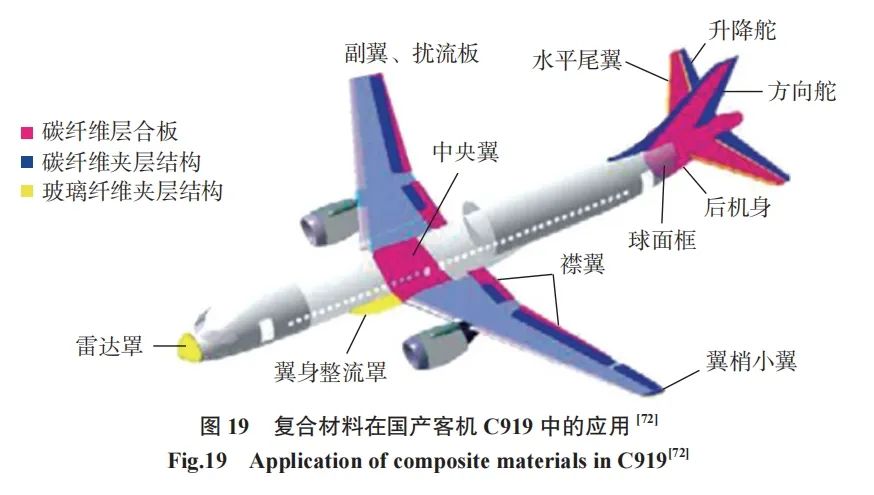
3.1 高性能复合材料
在航空航天领域,复合材料薄壁加筋结构的组元选择受多种因素影响。从纤维增强体的角度看,常用的复合材料有碳纤维和玻璃纤维复合材料。此外,还发展出了混杂纤维复合材料 [73–74],以碳纤维与玻璃纤维混杂增强复合材料为例,既有碳纤维复合材料的刚度、强度,又有玻璃纤维复合材料的韧性、断裂延伸率。这种混杂纤维复合材料,不仅能够节约成本,还可以通过对纤维及其体积分数的设计拓展复合材料的物理和机械性能,得到单一纤维无法获得的性质。
从基体的角度看,聚合物基复合材料可以分为热固性和热塑性两类,其中热固性聚合物基体在高温高压或添加催化剂的条件下固化,且固化后不再可塑,因此具有耐高温、抗腐蚀、高刚度等属性,但可回收性和加工性能较差。而热塑性聚合物基体能够在加热条件下熔融再加工,因此具有良好的可回收性,且具有较好的抗疲劳性能。目前,一些耐高温、高性能的热塑性聚合物基体,如聚醚醚酮、聚苯硫醚(PPS)、聚醚酰亚胺(PEI)等 [75] 在航空航天领域已有应用。
纤维、基体材料的材料属性决定结构设计中使用的材料本构模型,除这种材料 – 结构设计自由度外,二者之间的相互作用也会对结构工艺设计产生影响。如纤维与基体的浸润作用会影响制造环节的具体工艺形式及制造成本 [76],二者之间的热物理性质差异会引起成型过程中的分层、开裂等缺陷。因此,在进行材料选择与设计时,应综合考虑纤维、基体以及二者之间的相互作用,充分发挥复合材料的优势,以满足航空航天不同应用需求。
3.2 圆柱状薄壁加筋结构
圆柱状薄壁加筋结构通常由圆柱体薄壳和内 / 外部加强筋构成,常见于飞机圆柱形机身、火箭燃料罐、导弹筒等部件。图 20[77] 展示了一种飞机机身的薄壁加筋结构及其制造过程。针对圆柱薄壁加筋结构在航空航天领域的广泛应用,需要综合考虑结构使用过程中的多种载荷,如惯性载荷、温度载荷、外界环境影响等多种因素。在加强筋结构设计时需要考虑材料属性、加强筋数量、分布、尺寸等设计变量,以实现足够的强度和稳定性。
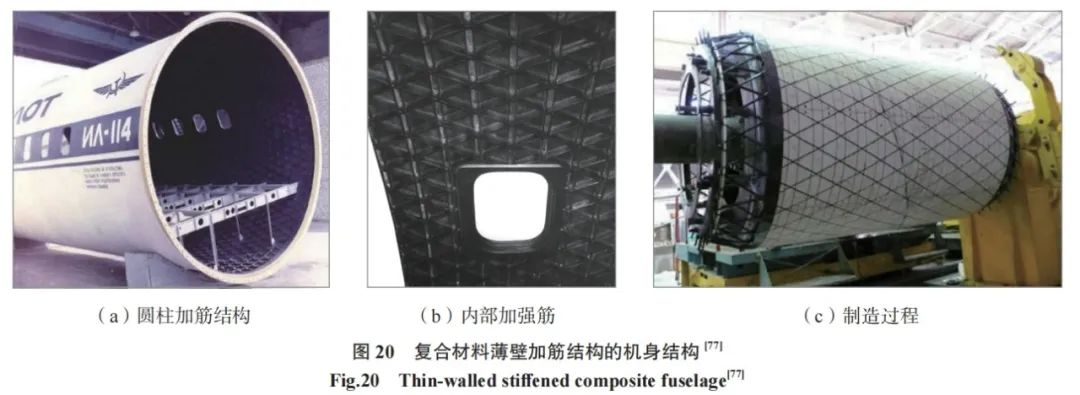
圆柱状薄壁加筋结构的制造过程常选用纤维缠绕成型工艺,该工艺尤其适用于回转结构件的生产制造。制造过程涉及材料准备、纤维铺放、切割、表面处理等多个工序,每个工序都需要保证精度,以实现生产质量和结构使用需求。此外,当前针对圆柱状薄壁加筋结构的设计制造,存在一些挑战和需求。例如,如何根据不同的工况和应力情况设计合适的加强筋结构,如何降低加强筋的重量、减少制造成本,如何提高加强筋的定位精度,如何保证结构的性能和质量稳定等问题。因此,对于圆柱状薄壁加筋结构的研究和发展,需要继续探索新的设计和制造方法,以满足不断变化的航空航天领域的需求和挑战。
3.3 板状薄壁加筋结构
板状薄壁加筋结构在航空航天领域的应用主要包括飞机机翼、火箭外壳、卫星结构等,能够提高大型平板结构的刚度和强度,同时减轻结构重量,提高飞机 / 航天器等的运载能力和效率,如图 21 所示 [78–79]。与圆柱薄壁加筋结构设计类似,在进行板状加筋结构设计时,需要综合考虑工作载荷类型和大小、环境影响等因素,结合先进的加强筋设计方法,实现薄壁加筋结构的刚度、强度。

在板状薄壁加筋结构的制造过程中,以纤维自动铺放技术为主的增材制造技术逐渐被应用于平板结构的生产制造。尽管纤维自动铺放技术能够有效提高单位体积纤维的生产制造成本,但是针对大尺寸结构件的一体成型能力和生产成本的降低仍然是制造方面的重点。为此,引入更加庞大、复杂的生产设备可以提高大尺寸结构件的生产能力。此外,利用现有流水线的机器人平台并采用多机协同的生产策略,能够降低设备安装成本。这些方法有助于加速平板结构制造的工艺流程,提高生产效率和质量。
3.4 不规则薄壁加筋承载结构
不规则薄壁加筋承载结构是一种具有非规则截面形状和加筋形式的薄壁结构,如图 22 所示 [80–81],其设计灵活性高于规则薄壁加筋结构,但也更加复杂,需要更多的分析和设计工作。目前,随着加强筋结构设计方法,尤其是拓扑优化及其他先进设计方法的发展,不规则结构、复杂曲筋的设计能力不断提高。
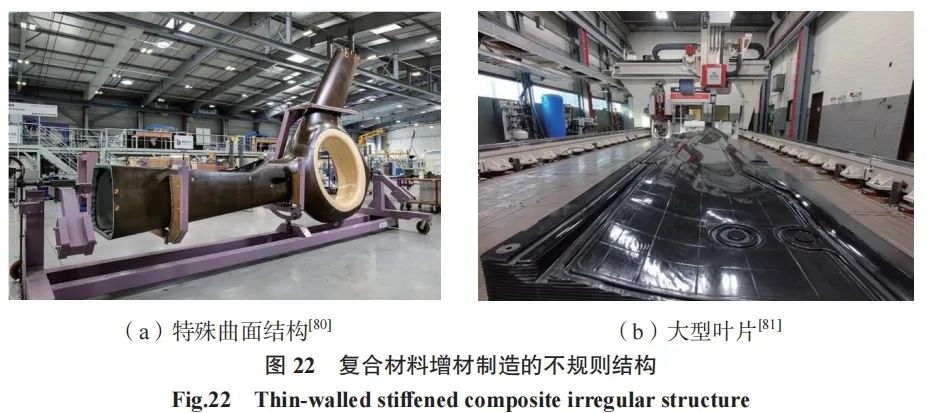
在制造方面,随着机械臂 / 机器人辅助设备的广泛应用,其灵活、准确的优势不断发挥,提高了复杂曲面结构、不规则薄壁加筋结构的生产能力。这类结构的加工灵活性主要取决于曲面本身及加强筋的结构复杂性,对于这种复杂加强筋结构,需要进行纤维铺放路径设计。特别是在机械臂式系统中,纤维铺放 / 打印的自由度大大提高,从而突破了传统纤维路径平行和等距限制。因此,通过优化加强筋结构的纤维位置和方向,可以实现机械性能的提高,这为薄壁结构的设计和制造提供了更广阔的空间和潜力。
04 结论
复合材料薄壁加筋结构作为轻质、高强的先进承载结构典型代表,其大规模应用推动了结构设计与制造技术的发展。目前平面、圆柱 / 圆锥、大曲率曲面等结构的加强筋结构设计与制造比较成熟,但对于复杂不可解析曲面、不规则结构等的薄壳结构加强筋设计与制造研究仍处于早期阶段。针对复合材料薄壁加筋结构设计与制造特点,提出以下趋势与挑战。
复合材料增材制造技术提高了纤维增强复合材料结构的制造能力,引入了新的结构、工艺设计自由度,围绕结构 – 工艺协同设计优化有以下发展趋势。
(1)复杂结构设计制造。复合材料薄壁加筋结构的复杂性和多样性在设计制造中提出了一些挑战。为了更好地应对这些挑战,需要研究复杂且不可解析空间曲面的数学表征及其加强筋设计,以实现任意空间曲面的性能优化。这需要进一步开发和完善数学模型和计算方法,以支持复杂曲面结构的优化设计。随着增材制造能力的不断提升,有望实现任意空间薄壁加筋构件的结构优化设计与制造成型。
(2)性能驱动工艺规划。增材制造工艺允许精确控制单束纤维的方向,使最终零件达到特定的机械性能,这意味着在进行加强筋 / 纤维路径设计时需要更仔细地规划和优化纤维方向,在真实工况与应力状态下,通过全局 / 局部纤维方向调控实现最终产品的全局 / 局部性能设计。此外,可以引入先进的多物理场仿真技术,如有限元分析和流体动力学模拟,来预测复合材料加强筋在使用过程中的应力分布、变形、损伤等情况,从而更好地进行纤维路径设计和工艺规划。
(3)多设计域协同优化。针对复合材料的各向异性,在结构、路径设计中引入具体材料属性以实现材料–结构–工艺三者协同设计。目前,基于组合材料的结构优化设计在提高结构强度、刚度、阻尼等方面已经取得了很大的进展,这对于实现复合材料薄壁加筋结构的轻量化设计具有非常重要的意义。同时,通过引入不同纤维及基体组合的具体属性,提高了设计自由度,以实现材料、结构、工艺的协同设计优化。
受制造设备硬件与复合材料本身性质的影响,也为结构及工艺设计带来了新的约束,面临以下挑战。
(1)结构几何形状。在进行复合材料薄壳结构加强筋设计时,结构的几何形状也是一个重要的考虑因素。例如,对于壳体最小曲率、纤维最小剪断距离、纤维预挤出长度等几何限制,需要进行精确计算和优化。此外,考虑到机械臂或其他自动化系统的灵活性,在进行结构设计时需要考虑具体几何形状以及实际制造的工作范围,对于复杂的形状可能需要考虑多机组协同设计。
(2)纤维排铺路径。在增材制造中,纤维排铺路径设计是非常重要的一环,因为它直接决定了增材制造零件的力学性能。同时,纤维路径不连续会增加纤维剪断、预挤出等过程,降低生产效率和质量。为了实现最佳的性能,需要在纤维铺放路径设计过程中考虑多种因素,如纤维的层叠顺序、纤维铺放路径、节点处理策略等。特别是对于复杂的结构,如曲面和不规则形状的零件,纤维铺放路径的设计需要综合考虑结构的力学性能、工艺参数的影响以及生产效率的要求等多方面因素。
(3)关键工艺参数。复合材料本身的材料属性除了由纤维及基体的种类决定外,两者之间的浸渍程度也是影响材料力学性能的关键因素。为了提高浸渍效果、提升复合材料力学性能,需要通过仿真或试验建立制造过程中打印温度、速度、预紧力等工艺参数与纤维 – 基体浸渍程度的映射关系,并以此为依据,对工艺参数进行优化。此外,通过使用机器学习等智能算法可以快速、准确找到最佳工艺参数组合,从而进一步提高复合材料的力学性能。
(4)特征处理策略。与均质材料成型不同,纤维特征如交叉、重叠等会出现不可忽略的材料堆积现象,表现为微观结构中的纤维断裂和宏观层面上的层厚变化,造成零件局部力学性能下降与加工几何精度变差。传统的纤维方向规划和路径设计往往难以处理这些特征,因此亟须发展新的纤维排布和特征处理策略。
参 考 文 献
[1] 雷煜东 , 詹梅 , 樊晓光 , 等 . 带筋薄壁构件成形制造技术的发展与展望 [J]. 西北工业大学学报 , 2022, 40(1): 1–17.
LEI Yudong, ZHAN Mei, FAN Xiaoguang, et al. A review on manufacturing technologies of thin-walled components with ribs[J]. Journal of Northwestern Polytechnical University, 2022, 40(1): 1–17.
[2] HAO P, WANG B, LI G, et al. Hybrid optimization of hierarchical stiffened shells based on smeared stiffener method and finite element method[J]. Thin-Walled Structures, 2014, 82: 46–54.
[3] WANG B, TIAN K, ZHOU C H, et al. Grid-pattern optimization framework of novel hierarchical stiffened shells allowing for imperfection sensitivity[J]. Aerospace Science and Technology, 2017, 62: 114–121.
[ 4 ] WA N G D , A B D A L L A M M , ZHANG W H. Buckling optimization design of curved stiffeners for grid-stiffened composite structures[J]. Composite Structures, 2017, 159: 656–666.
[5] WU Z M, WEAVER P M, RAJU G, et al. Buckling analysis and optimisation of variable angle tow composite plates[J]. ThinWalled Structures, 2012, 60: 163–172.
[6] BLOM A W, SETOODEH S, HOL J M A M, et al. Design of variable-stiffness conical shells for maximum fundamentaleigenfrequency[J]. Computers & Structures, 2008, 86(9): 870–878.
[7] PATRIKALAKIS N M, MAEKAWA T. Shape Interrogation for computer aided design and manufacturing[M]. Berlin: Springer Berlin Heidelberg, 2002.
[8] ZHAO W, KAPANIA R K. Buckling analysis of unitized curvilinearly stiffened composite panels[J]. Composite Structures, 2016, 135: 365–382.
[9] SLEMP W C H, BIRD R K, KAPANIA R K, et al. Design, optimization, and evaluation of integrally stiffened Al–7050 panel with curved stiffeners[J]. Journal of Aircraft, 2011, 48(4): 1163–1175.
[10] PASCHERO M, HYER M W. Improvement of axial buckling capacity of elliptical lattice cylinders[J]. AIAA Journal, 2011, 49(2): 396–410.
[11] LIU Y, SHIMODA M. Nonparametric shape optimization method for natural vibration design of stiffened shells[J]. Computers & Structures, 2015, 146: 20–31.
[12] HUGHES T J R, COTTRELL J A, BAZILEVS Y. Isogeometric analysis: CAD, finite elements, NURBS, exact geometry and mesh refinement[J]. Computer Methods in Applied Mechanics and Engineering, 2005, 194(39–41): 4135–4195.
[13] HAO P, WANG Y, TANG H, et al. A NURBS-based degenerated stiffener element for isogeometric static and buckling analysis[J]. Computer Methods in Applied Mechanics and Engineering, 2022, 398: 115245.
[14] ESCHENAUER H A, OLHOFF N. Topology optimization of continuum structures: A review[J]. Applied Mechanics Reviews, 2001, 54(4): 331–390.
[15] FERRARI F, SIGMUND O. Revisiting topology optimization with buckling constraints[J]. Structural and Multidisciplinary Optimization, 2019, 59(5): 1401–1415.
[16] DAPOGNY C, ESTEVEZ R, FAURE A, et al. Shape and topology optimization considering anisotropic features induced by additive manufacturing processes[J]. Computer Methods in Applied Mechanics and Engineering, 2019, 344: 626–665.
[17] WANG T, LI N Y, LINK G, et al. Load-dependent path planning method for 3D printing of continuous fiber reinforced plastics[J]. Composites Part A: Applied Science and Manufacturing, 2021, 140: 106181.
[18] BRAMPTON C J, WU K C, KIMH A. New optimization method for steered fiber composites using the level set method[J]. Structural and Multidisciplinary Optimization, 2015, 52(3): 493–505.
[19] LIU J, YU H. Concurrent deposition path planning and structural topology optimization for additive manufacturing[J]. Rapid Prototyping Journal, 2017, 23(5): 930–942.
[20] SUN Z Y, WANG Y G, GAO Z H, et al. Topology optimization of thin-walled structures with directional straight stiffeners[J]. Applied Mathematical Modelling, 2023, 113: 640–663.
[21] 王博 , 周子童 , 周演 , 等 . 薄壁结构多层级并发加筋拓扑优化研究 [J]. 计算力学学报 , 2021, 38(4): 487–497.
WANG Bo, ZHOU Zitong, ZHOU Yan, et al. Concurrent topology optimization of hierarchical stiffened thin-walled structures[J]. Chinese Journal of Computational Mechanics, 2021, 38(4): 487–497.
[22] MA X T, WANG F Y, AAGE N, et al. Generative design of stiffened plates based on homogenization method[J]. Structural and Multidisciplinary Optimization, 2021, 64(6): 3951–3969.
[23] DUGRÉ A, VADEAN A, CHAUSSÉE J. Challenges of using topology optimization for the design of pressurized stiffened panels[J]. Structural and Multidisciplinary Optimization, 2016, 53(2): 303–320.
[24] YANG K, TIAN Y, SHI T L, et al. A level set based density method for optimizing structures with curved grid stiffeners[J]. ComputerAided Design, 2022, 153: 103407.
[25] JIANG X D, LIU C, DU Z L, et al. A unified framework for explicit layout/topology optimization of thin-walled structures based on moving morphable components (MMC) method and adaptive ground structure approach[J]. Computer Methods in Applied Mechanics and Engineering, 2022, 396: 115047.
[26] WEI P, MA H T, WANG M Y. The stiffness spreading method for layout optimization of truss structures[J]. Structural and Multidisciplinary Optimization, 2014, 49(4): 667–682.
[27] WANG D, ABDALLA M M, WANG Z P, et al. Streamline stiffener path optimization (SSPO) for embedded stiffener layout design of non-uniform curved grid-stiffened composite (NCGC) structures[J]. Computer Methods in Applied Mechanics and Engineering, 2019, 344: 1021–1050.
[28] WANG D, ABDALLA M M, ZHANGW H. Sensitivity analysis for optimization design of non-uniform curved grid-stiffened composite (NCGC) structures[J]. Composite Structures, 2018, 193: 224–236.
[29] WANG D, YEO S Y, SU Z C, et al. Data-driven streamline stiffener path optimization (SSPO) for sparse stiffener layout design of nonuniform curved grid-stiffened composite (NCGC) structures[J]. Computer Methods in Applied Mechanics and Engineering, 2020, 365: 113001.
[30] 张坤鹏 , 郝鹏 , 段于辉 , 等 . 基于深度学习的多级曲线加筋壁板布局优化设计[J]. 中国舰船研究 , 2021, 16(4): 86–95.
ZHANG Kunpeng, HAO Peng, DUAN Yuhui, et al. Layout optimization design of hierarchical curvilinearly stiffened panels based on deep learning[J]. Chinese Journal of Ship Research, 2021, 16(4): 86–95.
[31] 董小虎 , 丁晓红 . 基于自适应成长法的周期性加筋结构拓扑优化设计方法 [J]. 中国机械工程 , 2018, 29(17): 2045–2051.
DONG Xiaohu, DING Xiaohong. Topology optimum design method for periodic stiffener structures based on adaptive growth method[J]. China Mechanical Engineering, 2018, 29(17): 2045–2051.
[32] MENG L, ZHANG J, HOU Y L, et al. Revisiting the Fibonacci spiral pattern for stiffening rib design[J]. International Journal of Mechanical Sciences, 2023, 246: 108131.
[33] DONG X H, DING X H, LI G J, et al. Stiffener layout optimization of plate and shell structures for buckling problem by adaptive growth method[J]. Structural and Multidisciplinary Optimization, 2020, 61(1): 301–318.
[34] 谢霞 , 邱冠雄 , 姜亚明 . 纤维缠绕技术的发展及研究现状 [J]. 天津工业大学学报 , 2004, 23(6): 19–22, 29.
XIE Xia, QIU Guanxiong, JIANG Yaming. Development and research situation of filament winding technology[J]. Journal of Tianjin Polytechnic University, 2004, 23(6): 19–22, 29.
[35] 史耀耀 , 阎龙 , 杨开平 . 先进复合材料带缠绕、带铺放成型技术 [J]. 航空制造技术 , 2010, 53(17): 32–36.
SHI Yaoyao, YAN Long, YANG Kaiping. Molding technology of tape winding and tape laying for advanced composites[J]. Aeronautical Manufacturing Technology, 2010, 53(17): 32–36.
[36] 许家忠 , 乔明 , 尤波 . 纤维缠绕复合材料成型原理及工艺 [M]. 北京 : 科学出版社 , 2013.
XU Jiazhong, QIAO Ming, YOU Bo. Forming principle and technology of fiber wound composite materials[M]. Beijing: Science Press, 2013.
[37] B U R A G O H A I N M , VELMURUGAN R. Study of filament wound grid-stiffened composite cylindrical structures[J]. Composite Structures, 2011, 93(2): 1031–1038.
[38] SAKATA K, BEN G. Development of fast fabrication method for cylindrical-shaped grids and mechanical properties of CFRP pressure vessel reinforced with cylindrical-shaped grids[J]. Advanced Composite Materials, 2016, 25(S1): 1–16.
[39] 蔡金刚 , 于柏峰 , 杨志忠 , 等 . 我国纤维缠绕技术及产业发展历程与现状 [J]. 玻璃钢 / 复合材料 , 2014(9): 42–51, 18.
CAI Jingang, YU Baifeng, YANG Zhizhong, et al. History and status of fiber winding technology and industry development in China[J]. Fiber Reinforced Plastics/Composited, 2014(9): 42–51, 18.
[40] 孔斌 , 顾杰斐 , 陈普会 , 等 . 变刚度复合材料结构的设计、制造与分析 [J]. 复合材料学报 , 2017, 34(10): 2121–2133.
KONG Bin, GU Jiefei, CHEN Puhui, et al. Design, manufacture and analysis of variablestiffness composite structures[J]. Acta Materiae Compositae Sinica, 2017, 34(10): 2121–2133.
[41] 王显峰 , 段少华 , 唐珊珊 , 等 . 复合材料自动铺放技术在航空航天领域的研究进展 [J]. 航空制造技术 , 2022, 65(16): 64–77.
WANG Xianfeng, DUAN Shaohua, TANG Shanshan, et al. Progress of composite automated placement technology in aviation field[J]. Aeronautical Manufacturing Technology, 2022, 65(16): 64–77.
[42] ELECTROIMPACT. Composite manufacturing[EB/OL]. (2017–03–25) [2023–03–15].
https://www.electroimpact.com/Products/Composites/Overview.aspx.
[43] REINFORCEDPLASTICS. Automating aerospace composites production with fibre placement[EB/OL]. (2011–06–28) [2023–03–15].
https://www.reinforcedplastics.com/content/features/automating-aerospace-compositesproduction-with-fibre-placement/.
[44] MARSH G. Automating aerospace composites production with fibre placement[J]. Reinforced Plastics, 2011, 55(3): 32–37.
[45] DEBOUT P, CHANAL H, DUC E. Tool path smoothing of a redundant machine: Application to automated fiber placement[J]. Computer-Aided Design, 2011, 43(2): 122–132.
[46] SACCO C, BAZ RADWAN A, ANDERSON A, et al. Machine learning incomposites manufacturing: A case study of Automated Fiber Placement inspection[J]. Composite Structures, 2020, 250: 112514.
[47] 李辰砂 , 张博明 , 武湛君 , 等 . 采用光纤传感器的专家系统实时监控复合材料固化成型过程的研究 [J]. 高技术通讯 , 2001, 11(8): 98–101, 97.
LI Chensha, ZHANG Boming, WU Zhanjun, et al. An investigation of monitoring the curing process of composite material by expert system with fiber optic sensor[J]. High Technology Letters, 2001, 11(8): 98–101, 97.
[48] ZHAO C, WANG X F, LIU X Y, et al. Study of integral hat-stiffened composite structures manufactured by automated fiber placement and co-curing process[J]. Composite Structures, 2020, 246: 112427.
[49] LI X, DUFTY J, PEARCE G M. Automation of tow wise modelling for automated fibre placement and filament wound composites[J]. Composites Part A: Applied Science and Manufacturing, 2021, 147: 106449.
[50] PENG X S, ZHANG M M, GUO Z C, et al. Investigation of processing parameters on tensile performance for FDM-printed carbon fiber reinforced polyamide 6 composites[J]. Composites Communications, 2020, 22: 100478.
[51] Z I A E E M , J O H N S O N J W, YOURDKHANI M. 3D printing of short-carbon-fiber-reinforced thermoset polymer composites via frontal polymerization[J]. ACS Applied Materials & Interfaces, 2022, 14(14): 16694–16702.
[52] A S I F S , C H A N S O R I A P, SHIRWAIKER R. Ultrasound-assisted vat photopolymerization 3D printing of preferentially organized carbon fiber reinforced polymer composites[J]. Journal of Manufacturing Processes, 2020, 56: 1340–1343.
[53] MATSUZAKI R, UEDA M, NAMIKI M, et al. Three-dimensional printing of continuousfiber composites by in-nozzle impregnation[J]. Scientific Reports, 2016, 6(1): 1–7.
[54] ZHANG G Q, WANG Y H, QIU W L, et al. Geometric characteristics of single bead fabricated by continuous fiber reinforced polymer composite additive manufacturing[J]. Materials Today: Proceedings, 2022, 70: 431–437.
[55] XU X G, REN H L, CHEN S Y, et al. Review on melt flow simulations for thermoplastics and their fiber reinforced composites in fused deposition modeling[J]. Journal of Manufacturing Processes, 2023, 92: 272–286.
[56] AKHOUNDI B, NABIPOUR M, HAJAMI F, et al. Calculating filament feed in thefused deposition modeling process to correctly print continuous fiber composites in curved paths[J]. Materials, 2020, 13(20): 4480.
[57] CHENG P, PENG Y, LI S X, et al. 3D printed continuous fiber reinforced composite lightweight structures: A review and outlook[J]. Composites Part B: Engineering, 2023, 250: 110450.
[58] FEDULOV B, FEDORENKO A, KHAZIEV A, et al. Optimization of parts manufactured using continuous fiber threedimensional printing technology[J]. Composites Part B: Engineering, 2021, 227: 109406.
[59] SUGIYAMA K, MATSUZAKI R, UEDA M, et al. 3D printing of composite sandwich structures using continuous carbon fiber and fiber tension[J]. Composites Part A: Applied Science and Manufacturing, 2018, 113: 114–121.
[60] PLOCHER J, WIOLAND J B, PANESAR A. Additive manufacturing with fibrereinforcement–design guidelines and investigation into the influence of infill patterns[J]. Rapid Prototyping Journal, 2022, 28(7): 1241–1259.
[61] SAVANDAIAH C. Continuous and short carbon fibre reinforced composites for extrusion-based additive manufacturing: processing and characterisation[D]. Linz: Johannes Kepler University Linz, 2022.
[62] SUZUKI T, FUKUSHIGE S, TSUNORI M. Load path visualization and fiber trajectory optimization for additive manufacturing of composites[J]. Additive Manufacturing, 2020, 31: 100942.
[63] 李涤尘 , 鲁中良 , 田小永 , 等 . 增材制造——面向航空航天制造的变革性技术[J]. 航空学报 , 2022, 43(4): 525387.
LI Dichen, LU Zhongliang, TIAN Xiaoyong, et al. Additive manufacturing—Revolutionary technology for leading aerospace manufacturing[J]. Acta Aeronautica et Astronautica Sinica, 2022, 43(4): 525387.
[64] 罗盟 , 田小永 , 尚俊凡 , 等 . 高性能纤维增强聚醚醚酮复合材料挤出成型增材制造现状与挑战 [J]. 航空制造技术 , 2020, 63(15): 39–47.
LUO Meng, TIAN Xiaoyong, SHANG Junfan, et al. Status and challenge of materials extrusion additive manufacturing for high-performance fiber reinforced poly (ether ether ketone) composites[J]. Aeronautical Manufacturing Technology, 2020, 63(15): 39–47.
[65] 刘彬 , 安卫龙 , 倪楠楠 . 国外热塑性复合材料工程应用现状 [J]. 航空制造技术 , 2021, 64(22): 80–90.
LIU Bin, AN Weilong, NI Nannan. Application status of thermoplastic composite materials in foreign engineering[J]. Aeronautical Manufacturing Technology, 2021, 64(22): 80–90.
[66] 徐永东 , 成来飞 , 张立同 , 等 . 连续纤维增韧碳化硅陶瓷基复合材料研究 [J]. 硅酸盐学报 , 2002, 30(2): 184–188.
XU Yongdong, CHENG Laifei, ZHANG Litong, et al. Research on continuous fiber reinforced silicon carbide composites[J]. Journal of the Chinese Ceramic Society, 2002, 30(2): 184–188.
[67] RAKHSHBAHAR M, SINAPIUS M. A novel approach: Combination of automated fiber placement (AFP) and additive layer manufacturing (ALM)[J]. Journal of Composites Science, 2018, 2(3): 42.
[68] GARDINER G. 3D-printed composite wind blades and aircraft, closer than you think[EB/OL]. (2018–01–29) [2023–03–19].
https://www.compositesworld.com/articles/3d-printedcomposite-wind-blades-and-aircraft-closer-thanyou-think.
[69] 贾振元 , 赖一楠 , 王福吉 , 等 . 复合材料构件制造关键基础科学问题——第 248期“双清论坛”学术综述 [J]. 中国科学基金 , 2021, 35(5): 764–773.
JIA Zhenyuan, LAI Yinan, WANG Fuji, et al. Key basic scientific questions in composite material parts manufacturing: An academic review of the 248 “Shuangqing forum”[J]. Bulletin of National Natural Science Foundation of China, 2021, 35(5): 764–773.
[70] 周正干 , 黄凤英 , 魏东 . 复合材料孔隙率超声检测方法综述 [J]. 航空制造技术 , 2009, 52(15): 104–106.
ZHOU Zhenggan, HUANG Fengying, WEI Dong. Ultrasonic testing method for porosity in composite[J]. Aeronautical Manufacturing Technology, 2009, 52(15): 104–106.
[71] 杜善义 . 先进复合材料与航空航天[J]. 复合材料学报 , 2007, 24(1): 1–12.DU Shanyi. Advanced composite materials and aerospace engineering[J]. Acta Materiae Compositae Sinica, 2007, 24(1): 1–12.
[72] 搜狐新闻 . 大飞机 C919 一飞冲天,新 材 料 功 不 可 没 [EB/OL]. (2017–12–11) [2023–03–17].
https://www.sohu.com/a/20987 3454_99896166.
Sohu News. Big plane C919 soars into the sky with new materials[EB/OL]. (2017–12–11) [2023–03–17].
https://www.sohu.com/a/20987 3454_99896166.
[73] 黄丽 . 聚合物复合材料 [M]. 2 版 . 北京 : 中国轻工业出版社 , 2012.
HUANG Li. Polymer composite material[M]. 2nd ed. Beijing: China Light Industry Press, 2012.
[74] 张博明 , 李嘉 , 李煦 . 混杂纤维复合材料最优纤维混杂比例及其应用研究进展[J]. 材料工程 , 2014, 42(7): 107–112.
ZHANG Boming, LI Jia, LI Xu. Optimum mix ratio of hybrid fiber reinforced polymer composites and their researching progress[J]. Journal of Materials Engineering, 2014, 42(7): 107–112.
[75] 张婷 . 高性能热塑性复合材料在大型客机结构件上的应用 [J]. 航空制造技术 , 2013, 56(15): 32–35.
ZHANG Ting. Applications of high performance thermoplastic composites for commercial airplane structural component[J]. Aeronautical Manufacturing Technology, 2013, 56(15): 32–35.
[76] LIU G, XIONG Y, ZHOU L M. Additive manufacturing of continuous fiber reinforced polymer composites: Design opportunities and novel applications[J]. Composites Communications, 2021, 27: 100907.
[77] VASILIEV V, RAZIN A. Development of geodesic composite aircraft structures[C]//28th International Congress of The Aeronautical Sciences(ICAS). Brisbane: Optimage Ltd, 2012.
[78] SLOAN J. The markets: Aerospace (2020)[EB/OL]. (2020–01–07) [2023–03–19]. https://www.compositesworld.com/articles/composites
原标题:《【复材资讯】复合材料薄壁加筋结构优化设计与增材制造综述》
本文为澎湃号作者或机构在澎湃新闻上传并发布,仅代表该作者或机构观点,不代表澎湃新闻的观点或立场,澎湃新闻仅提供信息发布平台。申请澎湃号请用电脑访问http://renzheng.thepaper.cn。

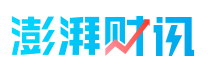
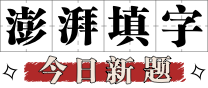
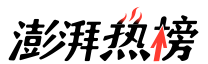
- 报料热线: 021-962866
- 报料邮箱: news@thepaper.cn
互联网新闻信息服务许可证:31120170006
增值电信业务经营许可证:沪B2-2017116
© 2014-2024 上海东方报业有限公司